Optimizing Jewelry Casting: A Guide to Outsourcing with Precision and Quality Control
The article explores the critical role of outsourcing jewelry casting in enhancing efficiency and qu…….
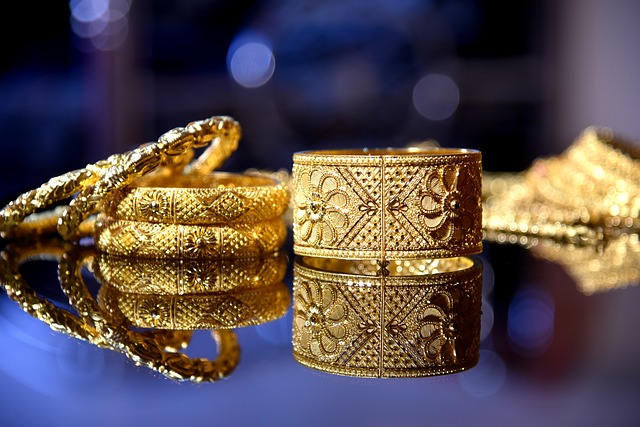
The article explores the critical role of outsourcing jewelry casting in enhancing efficiency and quality within the fine jewelry industry. It underscores the benefits of specialized casting techniques like lost-wax and investment casting for producing intricate, high-quality pieces, emphasizing the importance of precision, cost savings, and access to advanced equipment and expert craftsmanship that may not be available in-house. Outsourcing to experts ensures designers can focus on innovation and customer engagement while maintaining brand standards and satisfying consumer expectations. It is highlighted that selecting a reliable outsourcing partner with cutting-edge facilities and a strong reputation for quality and reliability, proficient in handling precious materials such as gold, silver, platinum, and palladium, is paramount. The article also touches on the complexities of managing logistics in outsourcing, requiring meticulous supply chain coordination and strategic planning to overcome geographical challenges and ensure timely delivery. Through adherence to stringent quality control measures and effective logistics strategies, jewelry brands can maintain their commitment to producing exceptional wearable art while navigating the outsourced casting process successfully.
Exploring the intricate world of jewelry casting, this article delves into the advantages and nuances of outsourcing this specialized craft. From the initial stages of selecting a reliable partner to the technical specifics of materials and methods, we provide a comprehensive guide on navigating the jewelry casting outsourcing landscape. Additionally, we address the critical challenges, including maintaining high-quality standards and mastering logistics management, ensuring your designs translate flawlessly from concept to wearable art. Whether you’re an independent designer or a brand, understanding these elements is key to successfully leveraging jewelry casting services.
- Understanding Jewelry Casting Outsourcing: An Overview of the Process and Benefits
- Evaluating Potential Jewelry Casting Partners: Key Factors for Successful Outsourcing
- The Technicalities of Jewelry Casting Outsourcing: Materials, Methods, and Precision
- Navigating the Challenges in Jewelry Casting Outsourcing: Quality Control and Logistics Management
Understanding Jewelry Casting Outsourcing: An Overview of the Process and Benefits
Jewelry casting outsourcing has become an integral aspect of the contemporary jewelry manufacturing industry, offering a blend of precision, efficiency, and cost-effectiveness that is hard to replicate in-house. The process of jewelry casting involves creating a mold from a wax or resin model of the desired piece of jewelry, which is then filled with molten metal to produce the final product. This technique, often utilizing lost-wax casting or investment casting methods, allows for intricate details and high-quality finishes that are consistent and repeatable.
Outsourcing this specialized process to experienced foundries brings several advantages. Firstly, it grants access to state-of-the-art equipment and expertise that may be cost-prohibitive for some jewelers to maintain internally. Secondly, it frees up valuable time and resources for designers and businesses to focus on other critical aspects of their operations, such as design, marketing, and customer engagement. Moreover, reputable outsourcing partners adhere to industry standards and regulations, ensuring that the final pieces not only meet but often exceed quality expectations. This reliability and the ability to scale production according to demand make jewelry casting outsourcing a compelling option for both emerging and established jewelry brands.
Evaluating Potential Jewelry Casting Partners: Key Factors for Successful Outsourcing
When considering outsourcing jewelry casting, businesses must meticulously evaluate potential partners to ensure the highest quality and reliability in their products. The selection process should prioritize partners with state-of-the-art casting facilities equipped with modern technology such as investment casting or lost-wax casting methods. These technologies are pivotal in creating intricate designs and fine details that are characteristic of high-end jewelry. Additionally, assess the partner’s expertise in handling different types of materials, including precious metals like gold, silver, and platinum, which are common in the jewelry industry. The ability to maintain consistency in casting is crucial for producing pieces that meet brand standards and consumer expectations.
Furthermore, a potential partner’s track record in terms of their experience in the field, market reputation, and history of successful collaborations with other brands are significant indicators of their reliability and quality of output. It is also imperative to consider the communication channels and protocols that the outsourcing partner employs. Efficient communication ensures that designs are accurately translated into physical products and that any issues can be promptly addressed, minimizing delays and ensuring a smooth operation. By carefully considering these factors, businesses can establish a fruitful partnership for jewelry casting that supports their growth and enhances their product line’s integrity.
The Technicalities of Jewelry Casting Outsourcing: Materials, Methods, and Precision
In the realm of fine jewelry production, jewelry casting is a meticulous process that demands precision and expertise. Outsourcing this intricate operation can be beneficial for businesses seeking to streamline their production and ensure high-quality results. The technicalities of jewelry casting outsourcing begin with the selection of materials; typically, silversmiths and goldsmiths use precious metals like gold, silver, platinum, and palladium, each with its own casting properties and alloy considerations. Outsourced casting facilities must be well-versed in handling these materials to produce consistent and durable pieces. The methods employed in jewelry casting outsourcing often include lost-wax casting, investment casting, and 3D printing, each offering distinct advantages in terms of detail, complexity, and efficiency. Lost-wax casting, for instance, is prized for its ability to capture fine details, while 3D printing allows for the production of complex designs that were once difficult to cast. Precision is paramount in these processes, as minor inaccuracies can result in flawed or unusable pieces. Outsourcing partners must possess advanced equipment and adhere to stringent quality control measures to meet the industry’s standards for dimensional accuracy, surface finish, and overall aesthetic appeal. By leveraging specialized outsourcing services, jewelry designers and manufacturers can focus on design innovation while ensuring that their products are crafted to the highest technical specifications.
Navigating the Challenges in Jewelry Casting Outsourcing: Quality Control and Logistics Management
In the realm of fine jewelry manufacturing, jewelry casting plays a pivotal role in translating intricate designs into wearable art. Outsourcing this process presents unique challenges that must be meticulously navigated to maintain the integrity of the final product. Quality control stands as a paramount concern; it ensures that the cast pieces adhere to the desired specifications and the brand’s quality standards. The precision of casting is influenced by factors such as material choice, mold making, and the application of investment or lost-wax techniques. Outsourcing partners must possess advanced capabilities in these areas, coupled with a rigorous quality control process that mirrors the brand’s internal practices.
Logistics management further complicates the outsourcing equation. Efficient handling and transportation of materials and finished products are essential to avoid damage and maintain timelines. The supply chain must be robust and responsive to disruptions, ensuring a seamless flow from the foundry to the designer and finally to the consumer. Coordination with suppliers across different geographical locations requires advanced planning and real-time tracking to mitigate potential delays or issues. By implementing stringent quality control measures and optimizing logistics strategies, jewelry brands can overcome the hurdles associated with outsourcing their casting needs while upholding the reputation and quality expected of their creations.