Navigating Jewelry Casting Challenges: A Guide to Materials, Technology, and Defect Prevention
Jewelry casting is a meticulous process where elaborate designs are transformed into wearable art th…….
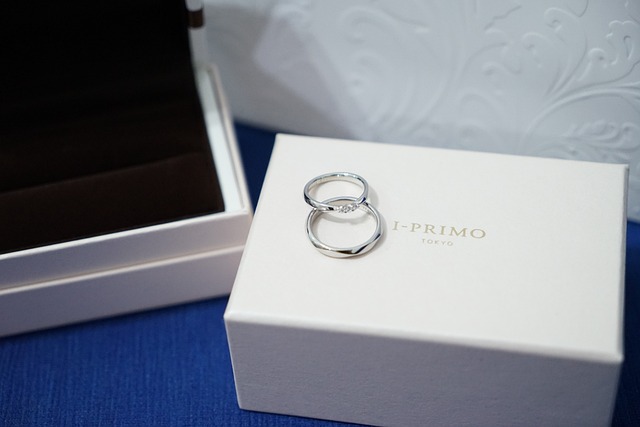
Jewelry casting is a meticulous process where elaborate designs are transformed into wearable art through precise material selection and expert craftsmanship. The choice of materials like sterling silver or gold alloys, each with distinct properties, affects the final product's quality and characteristics. The mold's material, whether wax, silicone, or metal, is critical for a defect-free replica of the design. Casting precision is influenced by the chosen casting method—lost-wax or investment casting—and the artisan's skill in managing the pouring process to prevent turbulence and defects. Post-casting stages of cleaning, finishing, and detailing are essential for refining the piece and ensuring its longevity and appearance. The evolution of jewelry casting incorporates technological innovations that refine design accuracy, detect potential issues before mold making, and streamline production with eco-friendly practices like 3D printing and CAD modeling. Mastery in these areas is crucial for producing high-quality jewelry with intricate details and unmatched diversity, underpinned by cutting-edge casting technology. The seamless integration of defect prevention during casting with expert finishing techniques post-casting is what sets exceptional jewelry apart.
Jewelry casting transforms intricate designs into tangible, wearable art. This article delves into the multifaceted challenges inherent in the jewelry casting process, offering insights into mastering this delicate craft. From selecting optimal materials to leveraging cutting-edge technologies, we explore the nuances of casting that ensure the highest quality pieces. Each section illuminates pivotal aspects of the process, from understanding the mechanics of casting to mastering defect prevention and refining techniques. Join us as we navigate the intricacies of jewelry casting, where precision meets artistry.
- Understanding the Casting Process in Jewelry Manufacturing
- Material Considerations and Their Impact on Casting Quality
- Technological Advancements and Their Role in Overcoming Casting Challenges
- Mastering Defect Prevention and Finishing Techniques in Jewelry Casting
Understanding the Casting Process in Jewelry Manufacturing
In the realm of jewelry manufacturing, the casting process is a critical technique that allows for intricate designs to be transformed into wearable art. This process involves pouring molten metal into a mold to create a solid piece, capturing the exact details of the design. To successfully execute jewelry casting, an understanding of various factors is essential. The choice of material—ranging from sterling silver to gold alloys—requires careful consideration due to differences in melting points and properties post-casting. The integrity of the mold, whether it be wax, silicone, or metal, plays a pivotal role in ensuring the casting process yields a precise replica of the original design without defects.
The precision of the casting process is influenced by several interdependent variables, including the type of casting method employed—such as lost-wax casting or investment casting—and the skill of the artisan overseeing the operation. The temperature and rate of metal pour must be controlled to avoid turbulence that could lead to air pockets or inaccuracies. Additionally, the post-casting processes like cleaning, finishing, and detailing are as critical as the initial pour; these steps remove any imperfections and enhance the piece’s aesthetic appeal and durability. Mastery of jewelry casting hinges on a deep understanding of these intricacies, making it a discipline that demands both technical precision and artisanal finesse.
Material Considerations and Their Impact on Casting Quality
In the realm of jewelry casting, material considerations play a pivotal role in determining the final quality and characteristics of the finished piece. The choice of material directly affects the casting process, as different metals have distinct melting points, viscosities, and reactive properties. For instance, sterling silver, an alloy of silver (92.5% pure silver) and copper, has a lower melting point compared to pure gold or platinum. This necessitates precise temperature control during the casting process to prevent material burn-off or defects such as cold shuts or misruns. Similarly, the density and thermal conductivity of the metal influence how heat is distributed within the mold, impacting the integrity of the casting. Gold, with its higher melting point and less reactive nature, requires more energy to melt and a longer heating cycle but yields castings with exceptional detail and durability. Additionally, materials like titanium or palladium offer unique challenges due to their high strength and complex alloying behaviors, which can affect the casting technique’s effectiveness if not properly managed. Understanding the nuances of each material is essential for jewelers and foundry operators to optimize casting parameters, ensuring the highest quality finish and minimizing post-casting processes like cleaning or filing.
Furthermore, the intricacies of jewelry design, particularly when it comes to small details or thin sections, further complicate the casting process. Delicate elements risk warping or distortion if the material isn’t cooled adequately after casting. The use of investment casting techniques, which involve creating a mold from a wax replica of the jewelry piece, demands meticulous attention to detail and a deep understanding of the chosen material’s properties. The investment material itself must be selected with care, as it interacts with the molten metal and affects the final surface finish. Jewelers must balance the need for high-quality casting with cost-effectiveness and practicality, ensuring that the end product not only meets aesthetic standards but is also durable and safe for wear. Mastering material considerations in jewelry casting is a testament to the artisan’s skill and the foundation upon which exceptional pieces are built.
Technological Advancements and Their Role in Overcoming Casting Challenges
In the realm of jewelry making, casting has long been a fundamental technique for transforming wax models into intricate metal pieces. The advent of technological advancements has significantly impacted this process, overcoming many of the challenges historically associated with jewelry casting. Modern technology has introduced precision instruments and sophisticated software that allow artisans to refine designs with greater accuracy and repeatability. These tools enable makers to simulate the casting process, identify potential issues before physical mold creation, and optimize patterns for the perfect flow of molten metal, thus minimizing defects such as air pockets or misruns. Moreover, advancements in foundry equipment now facilitate the use of a variety of materials, expanding the range of jewelry that can be produced with improved durability and finish.
The integration of digital technologies, particularly 3D printing and computer-aided design (CAD), has further revolutionized the casting process. CAD models allow for precise manipulation of designs, ensuring that the final cast piece closely matches the intended aesthetic. With 3D printing, jewelry designers can produce intricate patterns and molds with complex geometries that were previously difficult or impossible to create. This technology also reduces waste and shortens production time, making the casting process more cost-effective and environmentally friendly. As a result, jewelers are now able to push the boundaries of their creativity, producing pieces with unprecedented detail and diversity, all while leveraging technological advancements to overcome the traditional challenges of jewelry casting.
Mastering Defect Prevention and Finishing Techniques in Jewelry Casting
In the meticulous field of jewelry casting, mastering defect prevention and finishing techniques is paramount to achieving high-quality pieces. Casting jewelry involves pouring molten metal into a mold to create the desired shape, which can lead to various defects such as misruns, cold shuts, or porosity if not executed with precision. To mitigate these issues, casting professionals must meticulously prepare the wax models and molds, ensuring they are free of imperfections that could compromise the integrity of the final cast. The choice of materials, from the wax used for the model to the investment material for the mold, plays a critical role in determining the quality of the final product. Furthermore, controlling the temperature and flow rate of the molten metal during the casting process is essential to prevent turbulence that could lead to defects.
Once the casting process is complete, the focus shifts to finishing techniques, which are equally as crucial for the excellence of the jewelry piece. This stage involves a series of detailed processes, including cleaning, filing, sanding, and polishing. Each technique requires specific tools and expertise to smooth rough edges, remove any residual sprues or vents, and achieve a flawless surface that reflects light and showcases the design’s intricate details. The artisan’s skill in employing these finishing techniques can transform a cast piece from ordinary to extraordinary, ensuring that each item meets the high standards expected in fine jewelry casting. Mastery of defect prevention during casting and mastery of finishing techniques post-casting are interdependent; one cannot achieve excellence without excelling in the other. This synergy between process control and artisanal craftsmanship is what distinguishes exceptional jewelry from the ordinary.