Modern Artistry: The Impact of Jewelry Casting in Contemporary Design
Jewelry casting is a pivotal technique in modern jewelry design, merging the creative aspirations of…….
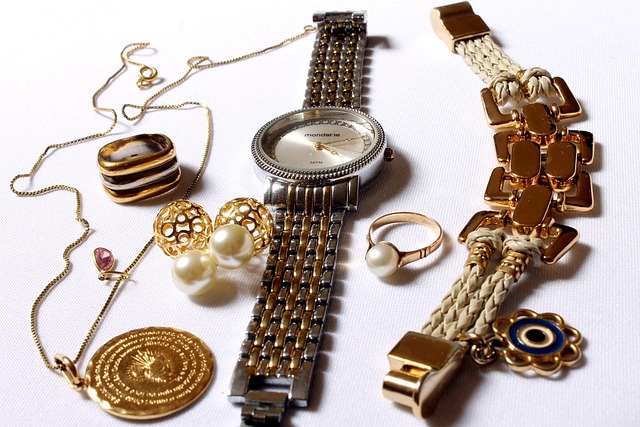
Jewelry casting is a pivotal technique in modern jewelry design, merging the creative aspirations of designers with the tangible outcomes of their artistic vision. This process involves creating a mold and pouring molten metal into it to form intricate and detailed pieces that are challenging to craft by hand alone. The precision and repeatability of casting make it ideal for both high-quality artisan work and mass production, allowing for complex designs with consistent quality. Contemporary jewelry crafters utilize this technique to innovate, experimenting with new materials and methods to produce visually striking and durable pieces. The versatility of casting accommodates a wide spectrum of styles, from minimalist to elaborate designs, all crafted with a high level of artisanship. Jewelry casting combines traditional methods like lost-wax casting with modern technologies such as 3D printing and CAD, enhancing design complexity and refining pieces before physical casting. The use of sustainable materials alongside traditional precious metals has expanded, offering stronger, more durable, and hypoallergenic jewelry options that meet contemporary consumer needs. This fusion of tradition and technology is shaping a new era in jewelry casting, one that offers limitless potential for design innovation. With roots in historical artistry, this craft continues to evolve, reflecting the legacy of pioneers like Alexander Calder, Georges Braque, and Rene Lalique, while pushing boundaries with eco-conscious practices. Today's jewelry artists skillfully blend traditional craftsmanship with modern aesthetics, ensuring that jewelry casting remains at the forefront of design excellence.
Jewelry casting stands at the intersection of artistry and craftsmanship, transforming intricate designs into wearable art. This article delves into the pivotal role of jewelry casting within modern jewelry design, exploring its evolution, technical nuances, and the luminaries who’ve shaped its trajectory. From the alchemy of molten metal to the finesse of detailed molds, the process of casting is a testament to human ingenuity in the realm of adornment. Join us as we trace the journey of this timeless technique through contemporary innovation, highlighting how jewelry casting continues to redefine the boundaries of design elegance and functionality.
- Understanding the Essence of Jewelry Casting in Contemporary Design
- The Evolution of Jewelry Casting Techniques and Materials
- The Process of Jewelry Casting: From Wax to Metal Masterpieces
- Pioneering Artists and Innovators in the Field of Cast Jewelry Design
Understanding the Essence of Jewelry Casting in Contemporary Design
In the realm of modern jewelry design, jewelry casting occupies a pivotal position, transforming intricate designs into tangible masterpieces. This process, which involves creating molds and pouring molten metal to shape the jewelry piece, allows designers to execute complex geometries and intricate details that would be challenging, if not impossible, to achieve by hand alone. The essence of jewelry casting lies in its ability to bridge the gap between the designer’s vision and the materialized outcome, enabling a level of precision and consistency that is crucial for mass production while maintaining high-quality standards. Contemporary designers harness this technique to push the boundaries of what is possible in jewelry design, incorporating advanced materials and innovative casting methods to produce pieces that are both aesthetically pleasing and durable. The versatility of jewelry casting allows for a wide array of designs, from minimalist bands to elaborate statement pieces, all crafted with an attention to detail that honors the artistry inherent in the process. As such, jewelry casting is not merely a production method but a cornerstone of contemporary jewelry design, offering a canvas upon which the creativity and skill of designers can be fully realized.
The Evolution of Jewelry Casting Techniques and Materials
The craft of jewelry casting has undergone significant advancements over the centuries, marking a remarkable evolution in the realm of modern jewelry design. Traditionally, artisans employed techniques such as lost-wax casting, which dates back to ancient civilizations and remains a staple method for creating intricate and detailed pieces. With the advent of new technologies, these age-old practices have been augmented by innovative processes like 3D printing and computer-aided design (CAD), allowing for greater precision and complexity in designs. These modern methods enable designers to transform conceptual sketches into tangible models before transitioning to actual casting, thus refining the intricacies of the jewelry without the risk of costly mistakes post-casting.
The materials used in jewelry casting have also seen a transformation, with traditional precious metals like gold and silver being complemented by more sustainable and diverse options. Today, casteries can work with a variety of alloys, including those that are recyclable or contain a higher percentage of reclaimed metals. The integration of new materials such as titanium and tungsten has expanded the horizons of jewelry casting, providing designers with a broader palette to express their creativity. Additionally, advancements in alloy composition have led to the creation of stronger, more durable, and hypoallergenic pieces, catering to the diverse needs and preferences of contemporary consumers. This synergy between traditional craftsmanship and modern innovation continues to propel jewelry casting into a new era of design possibilities.
The Process of Jewelry Casting: From Wax to Metal Masterpieces
Jewelry casting is an integral process in modern jewelry design, transforming intricate wax models into lasting metal masterpieces. The journey from conception to creation begins with the designer’s vision, which is meticulously sculpted in detail using specialized wax carving techniques. This wax model serves as a precise blueprint of the intended final piece, capturing every nuance and contour that will eventually be realized in metal.
Once the design is finalized, the casting process commences. The wax model is coated with a refractory material, creating a sturdy mold that can withstand the high temperatures required for melting the chosen metal. Silica or other advanced materials are commonly used for this purpose due to their ability to provide a durable and precise replica once the wax is removed. After the mold hardens, it is placed in a casting machine where the selected metal—such as gold, silver, or platinum—is melted and poured into the mold cavity. The metal fills every detail of the wax model’s design, resulting in a detailed cast that requires minimal post-processing. After cooling, the casting is carefully extracted, revealing a near-perfect replica of the original wax model. Any necessary finishing touches are then applied, such as polishing and setting gemstones, to bring the piece to its final luster and completion. This precise and technical process of jewelry casting enables designers to produce pieces with complex details and high-quality finishes, making it a cornerstone of contemporary jewelry manufacture.
Pioneering Artists and Innovators in the Field of Cast Jewelry Design
In the realm of modern jewelry design, jewelry casting has become a cornerstone technique, allowing for intricate and detailed pieces that push the boundaries of traditional craftsmanship. Pioneering artists like Alexander Calder and Georges Braque were among the early adopters of casting in their work, incorporating it into their sculptures and expanding its use beyond mere practicality. In jewelry design, the innovation continued with figures such as René Lalique, whose Art Nouveau creations redefined elegance and beauty through precise casting techniques. His use of glass and enamel casting set a new standard for fine jewelry, influencing countless designers who followed.
The 20th century saw further advancements with the advent of lost-wax casting, which enabled artists to achieve unprecedented levels of detail and complexity in their designs. Pioneers like Fritz Hartig and Wilhelm Richard Hütten were instrumental in refining this process, making it accessible to a wider audience. Contemporary jewelry designers have built upon these foundational techniques, integrating new materials and digital technologies to create jewelry casting that is both innovative and sustainable. Today’s vanguard of artists continues to explore the potential of casting, merging traditional craftsmanship with contemporary aesthetics to produce works that are as wearable as they are artful. The evolution of jewelry casting remains a testament to human creativity and the unending quest for beauty in small-scale sculpture. These artists not only preserve the legacy of their predecessors but also drive the field forward, ensuring that jewelry casting continues to be a vital aspect of modern jewelry design.