Mastering the Art of Lost-wax Casting in Modern Jewelry Design
The lost-wax casting process, a jewelry casting technique with a history spanning over five millenn…….
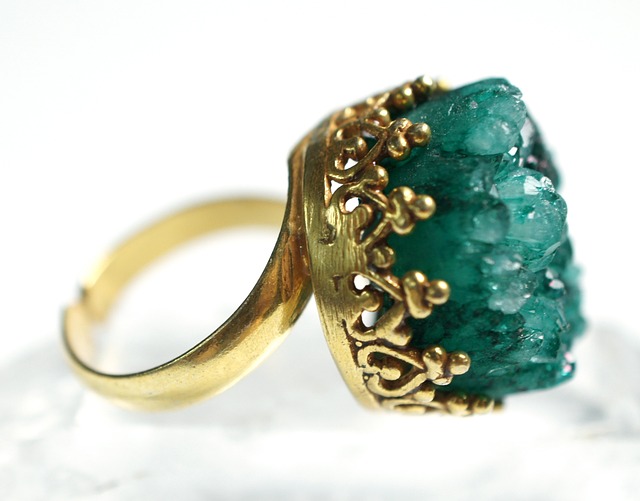
The lost-wax casting process, a jewelry casting technique with a history spanning over five millennia, remains a cornerstone of modern fine jewelry production. This ancient method involves creating a detailed wax model that captures the intricate design of the desired piece, which is then encased in refractory material to form a mold. After heating to harden into a robust shell, the wax is removed, leaving a cavity that accurately reflects the intended design. Molten metal is then poured into this cavity, replicating the original wax model's shape and intricate details as it cools and solidifies. Known as investment casting in the jewelry industry, this method ensures high precision and consistency, allowing for complex designs with a smooth and durable surface finish. Despite its historical roots, lost-wax casting has been significantly refined through advancements in technology, incorporating CAD software and 3D printing to craft the wax models. It remains a vital process in jewelry casting due to its precision and detail, despite the challenges of requiring skilled labor and specialized equipment, as well as considerations for environmental impact. The technique's ability to produce high-quality, detailed fine jewelry pieces continues to make it an essential method in the contemporary jewelry design industry.
Explore the intricate art of jewelry casting through the lens of tradition and innovation. The lost-wax casting process, an ancient technique with modern applications, has long been a cornerstone in the creation of exquisite fine jewelry. This article delves into its historical roots, evolution, and the meticulous steps involved in mastering this craft. We will uncover the advantages and hurdles faced by contemporary artisans and manufacturers who utilize this method, making “jewelry casting” a key term in understanding the enduring legacy and transformative potential of this timeless technique in the jewelry-making world.
- Overview of the Lost-wax Casting Process in Jewelry Making
- Historical Significance and Evolution of Lost-wax Casting in Jewelry Design
- Step-by-Step Guide to the Lost-wax Casting Technique for Crafting Fine Jewelry
- Benefits and Challenges of Lost-wax Casting for Contemporary Jewelry Artisans and Manufacturers
Overview of the Lost-wax Casting Process in Jewelry Making
The lost-wax casting process is an ancient technique integral to the jewelry casting craft, with a history that spans over 5,000 years. This intricate method involves creating a detailed wax model of the desired piece of jewelry. Artisans meticulously sculpt each element, capturing fine details that will later be mirrored in the final metal piece. The model is then coated with a refractory material, which, upon heating, forms a durable mold. This mold encases the wax, which is subsequently melted and drained out, leaving a cavity shaped exactly like the intended jewelry item. Molten metal is then poured into this cavity, filling it and taking the form of the original wax design. As the metal cools, it hardens into the exact replica of the model. The result is a finely detailed piece of jewelry with intricate designs and patterns that are consistent due to the precision of the lost-wax casting method. This technique, also known as investment casting, is highly valued in the jewelry industry for its ability to produce complex pieces with high levels of detail and finish. It allows jewelers to replicate designs with consistency and efficiency, making it a cornerstone of contemporary jewelry casting practices.
Historical Significance and Evolution of Lost-wax Casting in Jewelry Design
The lost-wax casting process, a technique as ancient as 3700 BCE, holds significant importance in the history of jewelry design. This method, also known as investment casting, has its roots in Mesoamerica and the Ancient Near East, where artisans crafted intricate pieces that have stood the test of time. Over millennia, the process evolved, with key developments during the Bronze Age in regions such as Egypt, China, and South Asia. The technique’s resilience is a testament to its efficiency and versatility, allowing for complex designs that would be challenging to achieve through other casting methods. As civilization advanced, so did the lost-wax casting process, with improvements in material refinement and mold precision enhancing the quality of cast jewelry. Today, this ancient art form continues to be a cornerstone of jewelry casting, enabling designers to create intricate pieces that blend tradition with modern innovation. The enduring nature of lost-wax casting underscores its pivotal role in the evolution of jewelry design, ensuring its place as a vital technique in contemporary artisanry and manufacturing.
Step-by-Step Guide to the Lost-wax Casting Technique for Crafting Fine Jewelry
The lost-wax casting technique, a cornerstone in the jewelry casting process, is a meticulous method that artisans employ to create intricate and detailed fine jewelry pieces. This ancient process, also known as investment casting, involves creating a mold from a wax model that accurately represents the final piece of jewelry. The procedure begins with the designer conceptualizing the jewelry design, which is then sculpted in wax using traditional hand-carving techniques or modern computer-aided design (CAD) software, followed by 3D printing to produce the wax model.
Once the wax model is complete, it undergoes a series of preparatory steps. The wax replica is attached to a sprue, which serves as a conduit for molten metal during the casting process. Additionally, a specific type of plaster called investment material is prepared and carefully packed around the wax model to form a durable mold. This mold envelops every detail of the jewelry design, ensuring that the final metal piece will replicate the intricacies of the original wax model. After the investment material hardens, the wax is melted away, leaving an exact negative cavity of the intended jewelry piece within the plaster mold.
The mold is then heated to a high temperature, allowing the designer to pour molten metal into the cavity. Silver, gold, or other metals are used, depending on the desired outcome and durability requirements. As the metal cools and solidifies, it takes the shape of the original wax model. Once the metal has solidified, the mold is broken away to reveal the raw jewelry piece. This raw casting is then cleaned and finished through various techniques such as grinding, sanding, and polishing to achieve a high-quality, refined surface. Finally, any additional details or settings are added, and the piece undergoes final inspection to ensure it meets the standards of fine jewelry craftsmanship. The lost-wax casting technique is integral to the jewelry casting process, enabling artisans to produce exquisite pieces with complex designs that are both functional and beautiful.
Benefits and Challenges of Lost-wax Casting for Contemporary Jewelry Artisans and Manufacturers
The lost-wax casting process, a technique with roots tracing back over 5,000 years, continues to be an invaluable method for contemporary jewelry artisans and manufacturers seeking precision and detail in their creations. This intricate process allows for the production of highly complex designs that would be nearly impossible to achieve through other casting methods. The benefit of lost-wax casting for jewelry lies in its ability to capture fine details, allowing for intricate patterns and textures that enhance the aesthetic appeal of the final piece. The high-quality surface finish obtainable through this process is unmatched, providing a smooth, durable, and consistent result every time. This uniformity is crucial for mass production as it ensures consistency across large quantities of jewelry.
Moreover, lost-wax casting significantly reduces the need for post-casting finishing, which saves time and labor costs for manufacturers. The process minimizes material waste by creating molds directly from a wax model, which also translates into cost savings. Additionally, the versatility of materials compatible with lost-wax casting, including precious metals like gold and silver, makes it an ideal choice for fine jewelry production. However, the challenges associated with this technique include its complexity, which requires skilled labor and specialized equipment, making it less accessible for smaller operations without significant investment. Furthermore, the process can be costly due to the materials used and the energy consumption in melting down the wax or metal, which has environmental implications. Despite these hurdles, the lost-wax casting process remains a cornerstone technique in jewelry manufacturing, celebrated for its precision and detail that continue to elevate contemporary designs.