Mastering the Art of Jewelry Casting: A Comprehensive Guide
The process of jewelry casting, specifically lost-wax casting, is a detailed art form central to cre…….
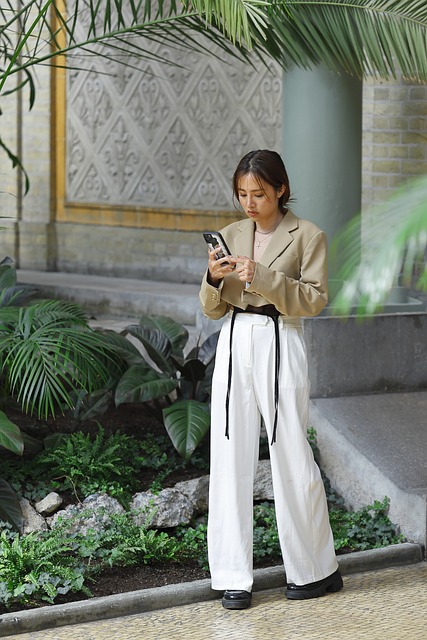
The process of jewelry casting, specifically lost-wax casting, is a detailed art form central to creating fine jewelry. Artisans craft intricate wax models that capture the exact design, which are then encased in a refractory material called investment to create an mold. This mold is heated until the wax melts away, leaving a cavity for molten metal—typically precious metals like gold, silver, platinum, or palladium—to fill. The high precision of this method ensures that the resulting castings have exceptional detail and surface finish, essential for high-quality jewelry.
Mold selection is crucial; investment molds are versatile and suitable for various metals, while lost-wax molds are preferred for complex designs with delicate details. The choice of metal alloy, including sterling silver, gold in different carats, platinum, or alternatives like Titanium and Palladium, affects the jewelry's durability, weight, and appearance. Each metal has its properties that impact the final piece's characteristics.
The casting process begins with designing the jewelry, which is then modeled in wax using either traditional hand-sculpting or advanced 3D printing technology. The wax model is connected to a sprue system for metal flow before being enclosed in investment material. After the investment hardens, the wax is burned out, leaving the mold ready for molten metal. The cast piece is then cleaned, finished, and polished to meet the designer's specifications.
Overall, jewelry casting combines traditional craftsmanship with modern technology to produce exquisite pieces that are true to the designer's vision. This meticulous process ensures that each piece of jewelry maintains its intricate details and high-quality finish, making lost-wax casting an indispensable method in the jewelry industry.
Embark on an enlightening journey into the intricate art of jewelry casting, a pivotal process that marries the timeless allure of ornamentation with modern precision. This comprehensive exploration will delve into the nuances of the casting techniques, including the traditional lost-wax method, the meticulous investment casting, and the robust full-mold casting. We’ll uncover the significance of wax models, the critical role of alloy selection, and the essential tools and safety measures that underpin this craft. From the innovative strides in technology to the environmental considerations shaping its future, this article will serve as a comprehensive guide for both aspiring artisans and seasoned jewelers. Join us as we shed light on the jewelry casting process and its integral part in the global jewelry industry.
- Understanding the Jewelry Casting Process
- Types of Molds Used in Jewelry Casting
- Materials Commonly Used for Jewelry Casting
- The Role of Wax Models in Casting Jewelry
Understanding the Jewelry Casting Process
The jewelry casting process is a sophisticated technique employed in the fine jewelry industry to create intricate and precise pieces from metal. This method, also known as lost-wax casting, involves several critical steps that transform a designer’s concept into a tangible object of beauty and craftsmanship. The process begins with the creation of a wax model, which accurately represents the desired jewelry piece in its entirety. This model is then attached to a sprue, a post that allows molten metal to fill the entire mold uniformly. The wax model is coated with a refractory material, which forms a durable and heat-resistant shell, known as a investment, around the wax. Once the investment hardens, the wax is melted away or ‘lost,’ leaving behind an empty cavity that is perfectly shaped like the original wax model.
The investment mold is then heated to a high temperature in a furnace designed for casting. The metal, typically gold, silver, platinum, or palladium, is melted and poured into the cavity. As the metal cools, it takes on the form of the void left by the wax. Care must be taken during this stage to ensure that the metal fills the mold completely without any air pockets or imperfections. Once the metal has solidified, the investment is broken away to reveal the raw casting. The resulting piece is then cleaned, finished, and polished to the designer’s specifications. In jewelry casting, precision and consistency are paramount; this process allows for the production of identical pieces with high detail and surface finish, making it a preferred method for fine jewelry artisans around the world.
Types of Molds Used in Jewelry Casting
In the intricate process of jewelry casting, the selection of the mold is paramount to achieving high-quality, precise pieces. The two primary types of molds used in this artisanal practice are investment molds and lost-wax molds. Investment molds involve creating a master model that is then covered with a silica-based refractory material known as investment. This hardens to form the mold, into which molten metal is poured to produce the jewelry item. The investment mold is particularly versatile, capable of replicating intricate details and complex designs with exceptional fidelity. It is suitable for a wide range of metals, including gold, silver, platinum, and palladium, making it a staple in the fine jewelry industry.
Lost-wax molds, on the other hand, are used when the design requires a detailed surface texture that investment casting may not perfectly capture. In this method, a wax replica of the desired jewelry piece is created and then encased in a refractory slurry. Once the slurry hardens, it forms the mold. Sprues and vents are strategically placed to allow for the flow of molten metal and the escape of gases during casting. The lost-wax process is ideal for pieces with delicate filigree or fine engravings, as it can accurately reproduce the original design’s subtleties without distortion or loss of detail. Both investment and lost-wax casting are integral to the jewelry industry, each offering unique advantages that cater to different needs within the craft.
Materials Commonly Used for Jewelry Casting
Jewelry casting is an intricate process that involves melting a material, typically a metal alloy, and pouring it into a mold to create a detailed replica of the desired design. The choice of material for jewelry casting significantly influences the final piece’s durability, weight, and aesthetic appeal. Among the materials commonly used in jewelry casting are sterling silver, gold, platinum, and various types of alloys. Sterling silver, an alloy consisting of 92.5% silver and 7.5% other metals, such as copper, is a popular choice due to its malleability and affordability. It provides a good balance between strength and the ability to capture fine details during the casting process. Gold, available in various carat weights, from 10K to 24K, is another widely used material. Higher carat weights offer a purer gold content but are softer and more prone to scratching; hence, they are often combined with other metals to enhance durability without compromising the precious metal’s luster and color.
Platinum, known for its strength and white color, has gained popularity in recent years as a material for fine jewelry due to its hypoallergenic properties and superior longevity. Alloys like Titanium and Palladium are also used for casting, offering alternatives to traditional precious metals. These materials provide a lighter weight option without sacrificing the strength and durability required for wearable pieces. Each material brings its unique characteristics and challenges to the casting process, requiring skillful manipulation by the artisan to achieve the desired outcome. The selection of the casting material is a critical decision that impacts both the functionality and the artistic expression of the finished jewelry piece.
The Role of Wax Models in Casting Jewelry
In the intricate process of jewelry casting, wax models play a pivotal role that is both foundational and critical to the final product’s quality and design. The creation of these models begins with the designer’s vision, which is meticulously translated into a detailed three-dimensional form using wax. This material is chosen for its compatibility with the casting process; it readily adheres to the investment material that will eventually create a mold around it. The artisan carefully sculpts each wax model by hand or utilizes advanced modeling software to generate a physical form through a 3D printer, which extrudes wax layer by layer to replicate the design’s intricate details. Once complete, the wax model undergoes a series of preparatory steps: it is attached to a sprue, a tree-like structure that allows molten metal to flow into all parts of the mold during casting. The model is then placed in a flask along with investment material, which, upon hardening, forms a durable and precise mold. This mold captures every nuance of the wax original, ensuring that the cast jewelry will mirror its intended design with precision and fineness. The investment mold is then heated to high temperatures, melting away the wax and leaving a cavity into which molten metal is poured. As the metal cools and solidifies, it takes on the exact shape of the original wax model, resulting in a piece of jewelry that embodies the designer’s vision with remarkable fidelity. This process, known as lost-wax casting, is a testament to the harmonious blend of artistry and technology in the creation of exquisite jewelry.