Mastering Precision: The Art and Science of Platinum Casting in Jewelry
Explore the artistry and precision of platinum casting techniques in jewelry making. This article d…….
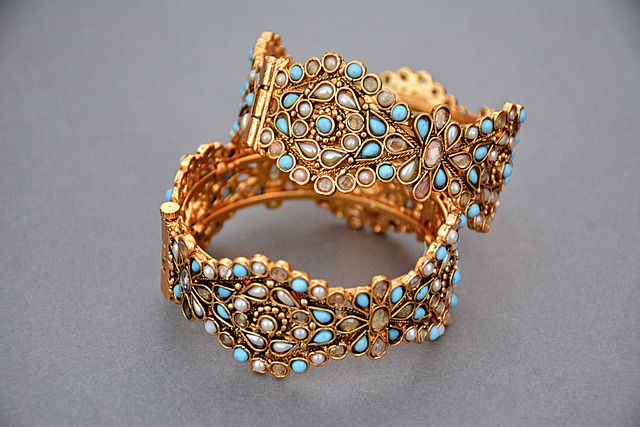
Explore the artistry and precision of platinum casting techniques in jewelry making. This article delves into mastering the craft, tracing the evolution from traditional to modern methods, and offering a deep dive into the unique properties of platinum alloys. Gain insights essential for achieving precision in your platinum jewelry creations with our comprehensive guide, ensuring your work stands out in the jewelry casting domain.
- Mastering Platinum Casting Techniques in Jewelry Making
- The Evolution of Platinum Casting: From Traditional to Modern Methods
- Material Insights: Understanding Platinum Alloys and Their Role in Casting
- Step-by-Step Guide to Achieving Precision in Platinum Jewelry Casting
Mastering Platinum Casting Techniques in Jewelry Making
Precision and skill are paramount in mastering platinum casting techniques within the jewelry-making craft. The process of jewelry casting with platinum, a dense and valuable metal, presents unique challenges due to its high melting point and inherent properties. Artisans must adhere to stringent safety protocols when working with platinum, ensuring proper ventilation and protective gear are in place. The intricate steps involved in lost-wax casting, a technique commonly employed for platinum jewelry, demand a deep understanding of material behavior at high temperatures and the ability to finely manipulate wax models to create precise molds.
To achieve successful castings, jewelers must select appropriate flasks and investment materials that are compatible with platinum’s composition, ensuring the integrity of the final piece. The heating phase requires precise control over the furnace, as an improper ramp-up or cooling rate can lead to undesirable outcomes like metal shrinkage, surface pitting, or even cracking. Post-casting, the artisan must skillfully handle the hot platinum to clean, file, and finish the piece without compromising its structural soundness. Through consistent practice and an understanding of the technical aspects unique to platinum casting, jewelers can produce exquisite, durable pieces that are both wearable works of art and testaments to their craftsmanship.
The Evolution of Platinum Casting: From Traditional to Modern Methods
The craft of platinum casting has undergone significant transformations over the centuries, transitioning from time-honored techniques to sophisticated modern processes that enhance precision and intricacy in jewelry design. Traditionally, platinum casting was a labor-intensive process, reliant on skills passed down through generations of artisans. The initial step involved creating a model in wax or another moldable material, which was then coated with a refractory material to withstand the high temperatures of molten platinum. This investment, as it’s known in the trade, would be heated in a crucible and carefully poured into the model to form the desired shape. The delicate nature of this process meant that only highly skilled crafters could execute it successfully, often leading to pieces that were not only exquisite but also rare.
Today, advancements in platinum casting techniques have revolutionized the industry. Computer-aided design (CAD) and computer-aided manufacturing (CAM) technologies have become integral tools for jewelry designers. These digital innovations allow for the precise creation of intricate designs that were once impossible or impractical to achieve. With CAD, a designer can conceptualize a piece in three dimensions on a screen, making adjustments with the click of a button. The design is then transformed into a physical object through 3D printing or direct metal laser sintering (DMLS), which creates a detailed plastic mold. This mold is filled with platinum using state-of-the-art casting machines, ensuring that each piece is replicated with remarkable accuracy and consistency. These modern methods not only streamline the production process but also democratize the ability to craft high-quality platinum jewelry, making it accessible to a wider audience while maintaining the luxurious and durable qualities synonymous with this precious metal.
Material Insights: Understanding Platinum Alloys and Their Role in Casting
Platinum alloys exhibit exceptional properties that make them highly sought after in various applications, with their role in jewelry casting being particularly significant. These alloys are known for their durability, resistance to tarnish, and luster, which contribute to the longevity and aesthetic appeal of fine jewelry pieces. The choice of material in casting is crucial for achieving the desired characteristics of the final product; platinum’s high melting point allows for intricate designs to be cast with precision and complexity without compromising on strength or integrity.
In the realm of jewelry casting, platinum alloys are often used in combination with other metals like palladium, gold, or cobalt to optimize workability and enhance properties such as ductility and malleability. The specific composition of the alloy can be tailored to meet the exacting standards required for different jewelry types, ensuring that each piece cast has a balance of aesthetic quality and functional durability. The casting process itself, whether it be investment casting or lost-wax casting, must be carefully managed to handle platinum’s unique characteristics; this involves precise temperature control during melting and a meticulous post-casting finishing process to achieve the flawless surface and polish that is emblematic of high-end jewelry. Understanding these material insights is essential for artisans and designers who aim to create exceptional pieces using platinum alloys in their casting endeavors.
Step-by-Step Guide to Achieving Precision in Platinum Jewelry Casting
In the realm of high-end jewelry making, achieving precision in platinum casting is both an art and a science. The process begins with meticulous preparation of the mold, which is crucial for ensuring the integrity and dimensionally accurate result. A skilled artisan starts by creating a detailed wax model that replicates the desired jeweled piece. This model is then attached to a sprue, a channel designed to deliver investment material into the mold during casting. The attachment point, known as the flask, is prepared with care to prevent any future weak spots. Once the wax model is secured, it is entirely encased in a silica-based slurry called investment. This investment hardens into a durable stone-like matrix that will form the exterior of the casting once cured.
After the investment has set, the assembly is heated in a casting machine to temperatures that melt the platinum alloy. The high precision control of these machines is essential for maintaining the correct temperature and flow rate for the metal to fill the mold without compromising the details of the design or the material’s integrity. As the molten platinum fills the mold, it replaces the wax, capturing every intricate detail. Once cooled, the investment is carefully chiseled away, revealing the raw casting. Subsequent hand-finishing and polishing are then performed to achieve the exquisite finish characteristic of premium platinum jewelry. Throughout this process, each step requires careful attention to detail, as slight variations can significantly impact the final product’s quality. Mastering these techniques not only demands technical proficiency but also a deep understanding of the material properties of platinum, ensuring that every piece cast is a testament to the precision and craftsmanship involved in the jewelry casting process.