Mastering Precision: The Art and Science of Modern Jewelry Casting
3D printing technology has revolutionized high-precision jewelry casting, enabling jewelers to creat…….
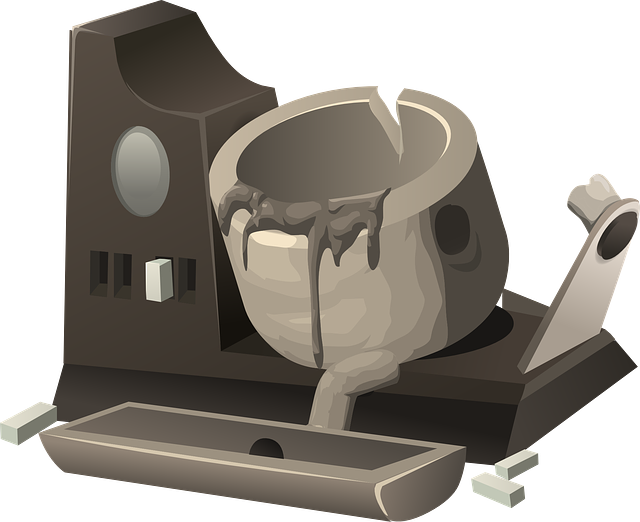
3D printing technology has revolutionized high-precision jewelry casting, enabling jewelers to create intricate designs that were previously impossible. The process involves crafting a detailed digital model, coating it with refractory material to form a durable mold, and then casting the piece using investment casting, a precise lost-wax technique. Selecting the right material—like gold, silver, or specialized alloys—ensures the integrity and beauty of the final product. Advanced CAD software and modern materials have elevated the art of jewelry making, allowing for greater complexity, sustainability, and personalization. The industry is also exploring eco-friendly alternatives and smart technology integration, such as sensors for authenticity and health monitoring, to stay at the forefront of innovation and ethical practices. This fusion of tradition with cutting-edge tech in jewelry casting has set new standards for quality and complexity, ensuring that each piece reflects the pinnacle of luxury craftsmanship.
Explore the intricate realm of high-precision jewelry casting, a meticulous craft that marries artistry with advanced technology. This article delves into the nuanced techniques and materials employed in this exquisite process, tracing its evolution from time-honored methods to cutting-edge precision technologies. Gain insights into the step-by-step intricacies of casting flawless pieces, and uncover innovative advancements that are shaping the future of jewelry design. Join us on this journey through the artistry and science behind creating gems that transcend beauty and enter the realm of high-precision craftsmanship.
- Understanding the Art of High-Precision Jewelry Casting: A Closer Look at Techniques and Materials
- The Evolution of Jewelry Casting: From Traditional Methods to Advanced Precision Technologies
- Mastering the Process: Step-by-Step Guide to High-Precision Jewelry Casting
- Innovations in High-Precision Jewelry Casting: Materials, Designs, and Future Trends
Understanding the Art of High-Precision Jewelry Casting: A Closer Look at Techniques and Materials
High-precision jewelry casting is a meticulous craft that demands exceptional skill and a thorough understanding of both traditional and modern techniques. The process begins with the creation of a precise model, often through 3D printing technology, which accurately represents the desired piece of jewelry. This digital innovation has revolutionized the jewelry industry, allowing for intricate designs that were once difficult or impossible to achieve. The model is then covered in a refractory material, forming a mold that can withstand high temperatures without deformation.
Artisans carefully select materials such as gold, silver, platinum, and various alloys for casting. The choice of material not only influences the durability and longevity of the final product but also its luster, weight, and malleability. Investment casting, a lost-wax technique, is widely used in high-precision jewelry casting due to its ability to produce complex geometries with fine details. In this method, a wax replica of the jewelry item is assembled on a tree-like structure within a shell of refractory material. Once the investment sets, it is heated to melt away the wax, leaving a cavity exact in shape to the original model. Molten metal is then poured into the cavity, filling it and taking the form of the jewelry piece as it cools. This process, when executed with precision, yields exquisite pieces with a high level of detail and finish, making it an essential technique for jewelers and designers aiming to produce high-quality, bespoke jewelry.
The Evolution of Jewelry Casting: From Traditional Methods to Advanced Precision Technologies
Jewelry casting has a rich history that spans millennia, with its origins tracing back to ancient civilizations. Traditional methods, such as lost-wax casting, have been refined over generations, allowing artisans to create intricate designs with remarkable consistency. These traditional techniques laid the groundwork for modern jewelry casting, which has evolved significantly due to advancements in technology and precision engineering.
Today, the field of high-precision jewelry casting is marked by a fusion of time-honored craftsmanship and cutting-edge technology. The advent of technologies like 3D printing and advanced computer-aided design (CAD) software has revolutionized the industry. These tools enable designers to visualize and fine-tune their creations before actualizing them in metal with unprecedented detail and accuracy. Moreover, innovations such as digital casting technology have reduced waste and increased the efficiency of the casting process. The result is a leap in the ability to produce jewelry that is not only beautiful but also more sustainable and precise than ever before. This evolution ensures that jewelry casting continues to meet the evolving demands of consumers and designers alike, setting a new standard for quality and intricacy in the world of fine jewelry.
Mastering the Process: Step-by-Step Guide to High-Precision Jewelry Casting
Mastering the art of high-precision jewelry casting involves a meticulous process that demands both technical skill and artistic finesse. The initial step in this intricate procedure is the creation of a precise model or mold, often achieved through techniques such as 3D printing or traditional wax carving. This model serves as a direct representation of the desired final piece, capturing every facet and detail with exactness. Once the model is complete, it undergoes investment casting, whereby it is encased in a heat-resistant material known as investment. This step ensures that when the metal is poured, it fills the mold accurately without distortion, preserving the intricate design elements of the jewelry piece.
The pouring phase is critical and requires precise control over temperature and flow rate to avoid air bubbles or imperfections in the casting. Silicon, bronze, or steel molds are typically used for their durability and ability to withstand high temperatures without deforming. The choice of metal alloy is also significant; gold, silver, platinum, and palladium each have distinct melting points and properties that must be considered to achieve the highest level of precision. After the metal has cooled and the investment is removed, the resulting casting requires careful finishing, which includes filing, polishing, and sometimes setting with gemstones. This final stage transforms the raw casting into a stunning piece of high-precision jewelry, ready to adorn and captivate. Throughout this process, consistency and precision are paramount, ensuring that each piece meets the stringent standards required for luxury jewelry.
Innovations in High-Precision Jewelry Casting: Materials, Designs, and Future Trends
The field of high-precision jewelry casting has seen significant advancements, particularly in materials and design techniques. Modern jewelry casting now leverages advanced alloys such as titanium and precious metals like gold and platinum with higher purity levels, allowing for more durable and hypoallergenic pieces. These materials are chosen not only for their aesthetic appeal but also for their ability to retain fine details in intricate designs. The use of computer-aided design (CAD) software has revolutionized the way designers approach jewelry making. It enables them to create complex, multi-faceted models that can be translated into physical form with remarkable accuracy through processes like lost-wax casting. This technology not only enhances the precision of the final product but also speeds up the production time, making it a viable option for both bespoke and mass-produced jewelry.
As the industry continues to evolve, there is a growing emphasis on sustainability and ethical practices in jewelry casting. Innovations are being driven by the integration of recyclable materials and energy-efficient casting methods. Additionally, the application of 3D printing technology in the pre-casting stage is becoming more prevalent, allowing for prototyping and customization that were previously difficult to achieve. The future of high-precision jewelry casting promises even greater personalization and environmental responsibility. Designers are exploring the use of biodegradable materials and zero-waste designs, ensuring that the beauty of jewelry does not come at the expense of the planet. With a focus on incorporating smart technology, such as embedded sensors for gemstone authentication or to monitor wearer health, the jewelry casting industry is poised to offer not just adornments but also companions with functionality beyond mere aesthetics.