Mastering Jewelry Casting: The Art and Science of Centrifugal Techniques
Centrifugal casting is transforming the jewelry casting industry by providing a technique that offe…….
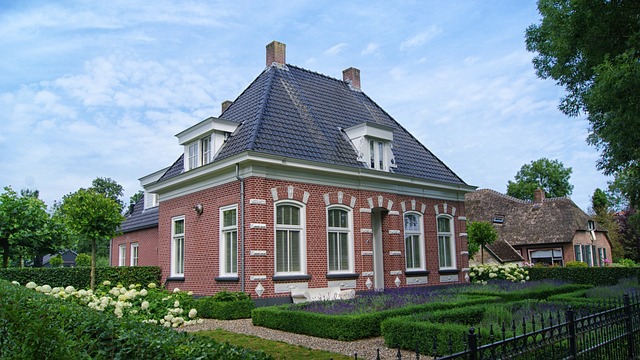
Centrifugal casting is transforming the jewelry casting industry by providing a technique that offers unparalleled precision and consistency, surpassing traditional methods like investment or lost-wax casting. This modern approach uses centrifugal force to distribute molten metal into molds, resulting in high-quality castings with minimal porosity and a remarkable level of detail fidelity. The process involves creating a wax or resin model, fixing it to a rotating arm within a flask, sealing the flask, and then applying centrifugal force to fill the mold with metal during casting. This method is particularly advantageous for small to medium-sized production runs, offering cost savings and increased efficiency, and leading to jewelry that requires minimal post-processing, thereby enhancing its durability and complexity. Artisans utilizing this technique consistently achieve better product quality and consistency, which positions them well in the competitive jewelry market. Centrifugal casting is a game-changer, enabling jewelers to produce intricate designs with diverse materials, including those not typically amenable to traditional casting methods, and facilitating both large-scale production and bespoke artisanal pieces. This technique's efficiency, adaptability, and ability to push design boundaries make it a cornerstone of contemporary jewelry production, marrying tradition with modern technology for superior results.
Centrifugal casting has revolutionized the jewelry industry by offering a precise and efficient method for creating intricate designs. This article delves into the intricacies of centrifugal casting, a technique that significantly enhances the quality and detail of jewelry pieces. We will explore its unique process, the advantages it presents over traditional casting methods, and how it can be applied to various jewelry types. A step-by-step guide will also provide insights on executing this technique effectively, ensuring high-quality finishes in jewelry design. Join us as we examine the transformative impact of centrifugal casting in modern jewelry production.
- Unraveling the Process of Jewelry Casting: An Overview of Centrifugal Casting Techniques
- The Advantages and Applications of Centrifugal Casting in Jewelry Manufacturing
- Step-by-Step Guide to Executing a Successful Centrifugal Casting in Jewelry Making
- Mastering Precision and Detail: Tips for Achieving High-Quality Finishes with Centrifugal Casting in Jewelry Design
Unraveling the Process of Jewelry Casting: An Overview of Centrifugal Casting Techniques
Centrifugal casting is a technique in jewelry production that offers precision and intricate detail, setting it apart from traditional casting methods. This process leverages centrifugal force to distribute metal evenly across a mold, resulting in high-quality castings with minimal porosity. The technique begins with the creation of a wax or resin model, which is then attached to a rotating arm within a flask. Once the flask is sealed, it is placed inside a centrifuge. As the centrifuge spins, the centrifugal force ejects molten metal into every crevice of the mold, replicating the model with remarkable accuracy. This method eliminates the need for investment or lost-wax processes, making it a cost-effective and efficient option for small to medium-sized jewelry production runs. The result is a near-perfect cast that requires less post-processing compared to other casting techniques. Centrifugal casting in jewelry making not only enhances the durability of the final piece but also allows for the use of more complex and detailed designs, which are otherwise challenging to achieve with conventional casting methods. Jewelry crafters who employ centrifugal casting often experience an improvement in the consistency and quality of their castings, leading to a competitive edge in the jewelry market.
The Advantages and Applications of Centrifugal Casting in Jewelry Manufacturing
Centrifugal casting, a technique that harnesses centrifugal force to fill molds with molten metal, has revolutionized the jewelry casting industry. This method is particularly advantageous due to its ability to produce intricate and complex designs with a high degree of consistency and precision. The centrifugal force compacts the metal against the mold walls, ensuring that even the most detailed patterns are filled entirely and accurately, eliminating the need for secondary finishing processes. As a result, jewelry pieces cast using this technique exhibit superior surface finishes and dimensional accuracy. Moreover, the high-speed rotation of the casting machine during the process leads to a reduction in porosity and internal stresses within the metal, which is crucial for durable and long-lasting jewelry items. This not only enhances the aesthetic appeal but also the functionality of the final product.
In terms of applications, centrifugal casting is widely used across the jewelry manufacturing spectrum, from mass production to artisanal craftsmanship. It is particularly beneficial for producing rings, bangles, and other circular designs where symmetry and surface quality are paramount. The method allows for the efficient casting of larger pieces without compromising on detail or integrity. Additionally, it enables the creation of jewelry with unusual materials, such as titanium or tungsten, which might be challenging through traditional casting methods. The versatility and efficiency of centrifugal casting in jewelry production make it an indispensable tool for contemporary jewelers seeking to expand their design capabilities and meet the growing demands of the market.
Step-by-Step Guide to Executing a Successful Centrifugal Casting in Jewelry Making
Centrifugal casting is a pivotal technique in the jewelry-making process, offering intricate designs and high precision. To execute a successful centrifugal casting in jewelry production, adherence to precise steps is crucial. The process begins with preparing the mold, ensuring it is designed to accommodate the desired shape of the final piece. Carefully choose materials for the mold that complement the metal you intend to cast, as this will affect the detail and durability of the finished product.
Once the mold is prepared, the next step involves loading the casting machine with the chosen material, typically a molten metal alloy suitable for the jewelry item. The machine operates by forcing metal through a nozzle at high speed using centrifugal force, which fills the mold evenly and eliminates air pockets that could compromise the piece’s integrity. It is vital to control the speed of the casting process and the temperature of the metal to achieve the correct density and surface finish. After the casting process is complete, the metal must cool gradually within the mold to prevent warping or cracking. Post-casting, the jewelry piece is removed from the mold and subjected to additional processes such as cutting, filing, sanding, and polishing to refine its shape and luster. Throughout this procedure, maintaining clean and well-maintained equipment is essential for consistent results and the longevity of your tools and molds. By meticulously following these steps and paying close attention to detail at each stage, jewelers can produce high-quality castings that showcase the intricate beauty and elegance of centrifugal casting in jewelry making.
Mastering Precision and Detail: Tips for Achieving High-Quality Finishes with Centrifugal Casting in Jewelry Design
Centrifugal casting has become an indispensable technique in the realm of jewelry production, renowned for its ability to produce intricate and detailed designs with high precision. To achieve the finest finishes in jewelry casting, artisans must master several key factors. The centrifugal force applied during the casting process ensures that the metal flows out evenly, filling the mold consistently, which is crucial for preventing defects such as porosity or air pockets that can compromise the integrity of the final piece.
Precision in centrifugal casting begins with the preparation of the mold and the choice of material. The design of the mold must be precise to accommodate the centrifugal force without distortion, ensuring that the metal takes the exact shape desired. Artisans should also select alloys that are well-suited for centrifugal casting, as this can significantly impact the quality and durability of the finished jewelry. Additionally, controlling the temperature and flow rate of the molten metal is vital to prevent overheating or solidification anomalies. Attention to detail in every step of the process, from mold preparation to post-casting treatment, will yield high-quality, intricate pieces that showcase the beauty and elegance inherent in jewelry casting techniques. By adhering to these guidelines, jewelers can produce exquisite, detailed jewelry with a surface finish that rivals traditional casting methods, ensuring their creations stand out in the market.