Mastering Jewelry Casting: Essential Tools for Lost-Wax Techniques
Lost-wax casting, an ancient art refined over centuries, is a cornerstone in jewelry making and fine…….
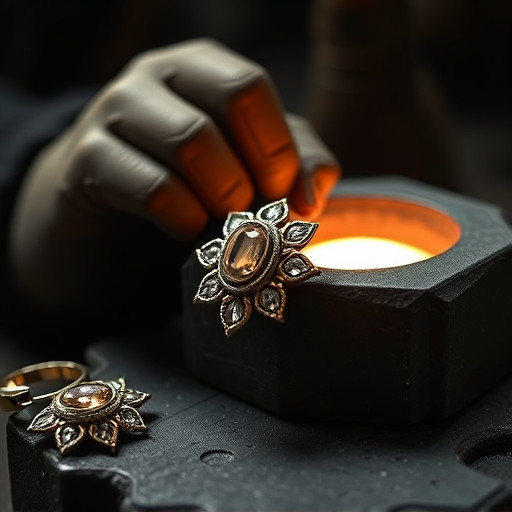
Lost-wax casting, an ancient art refined over centuries, is a cornerstone in jewelry making and fine arts. This meticulous process involves creating wax models with intricate details, encasing them in ceramic, and melting away the wax to create precise metal replicas. Essential tools include specialized wax models, injection molding machines, sculpting instruments, sprue caps, pour cups, and flux. Digital design software has transformed the process by providing advanced 3D modeling tools for complex geometric shapes and patterns, streamlining iterative design processes, and ensuring accurate models. Wax carving techniques, employing X-act knives, dental tools, and wax carving machines, create intricate designs with precision. These methods form the bedrock for successful jewelry casting in today's market.
Unleash your creativity with the ancient art of lost-wax casting, a fundamental process in jewelry making. This intricate method allows designers to bring their designs to life with remarkable precision and detail. In this comprehensive guide, we explore the tools and techniques that empower jewelry artisans. From understanding the fundamentals to mastering digital design software and wax carving, you’ll discover the secrets behind successful jewelry casting. Learn how to choose the ideal wax and master post-casting practices for breathtaking results.
- Understanding Lost-Wax Casting: A Brief Overview
- Essential Tools for Jewelry Designers and Makers
- Digital Design Software: Creating Accurate Models
- Wax Carving and Modeling Techniques
Understanding Lost-Wax Casting: A Brief Overview
Lost-wax casting is an ancient technique that has been perfected over centuries, becoming a cornerstone in the world of jewelry making and other fine arts. This intricate process involves creating a wax model of the desired object, which is then encased in a ceramic material (or ‘mold’) before being melted away, leaving behind an empty space in the shape of the original wax pattern. This negative space is subsequently filled with metal to create a precise replica, making it a popular method for jewelry casting.
By using this method, artisans can achieve remarkable detail and complexity in their designs, as the wax allows for intricate carvings and structures that are challenging (and sometimes impossible) to replicate in other casting techniques. It’s a meticulous process that demands skill and precision but offers unparalleled results, making it a sought-after approach in the production of high-quality jewelry and artistic sculptures.
Essential Tools for Jewelry Designers and Makers
For jewelry designers and makers, losing-wax casting is a powerful tool that allows for intricate and precise creations. Essential tools for this process include specialized wax models, injection molding machines, and various sculpting instruments. Wax models serve as the master pattern, enabling designers to craft detailed designs with precision. These models are then invested in ceramic or metal to create a mold, facilitating the pouring of molten metal, such as silver or gold, in the jewelry casting process.
Injection molding machines play a pivotal role by forcing melted wax into molds under high pressure, ensuring consistent and detailed results. Sculpting tools, including knives, scrapers, and files, are indispensable for refining wax models and achieving complex shapes and textures. In addition to these core components, other important equipment includes sprue caps, pour cups, and flux, which aid in the metal filling process, ensuring successful jewelry casting outcomes.
Digital Design Software: Creating Accurate Models
Digital design software has revolutionized the way jewelry designers approach the process of creating intricate pieces for jewelry casting. With advanced 3D modeling tools, artists can bring their visions to life with remarkable precision and detail. These programs allow for the creation of complex geometric shapes and intricate patterns that were once challenging or time-consuming to achieve manually.
By utilizing digital design software, jewelry makers can quickly iterate designs, experiment with different materials, and ensure accurate models for the lost-wax casting process. This technology has made jewelry casting more accessible and efficient, enabling designers to focus on their creativity rather than the technical limitations of traditional methods.
Wax Carving and Modeling Techniques
Wax carving is a precise art that forms the foundation for successful jewelry casting. This technique involves sculpting the desired design in wax, allowing for intricate details and complex geometries. Artisans use various tools like X-act knives, dental tools, and specialized wax carving machines to create models with exceptional accuracy. The process demands skill and patience, especially when crafting fine details such as textures or delicate curves.
Modeling techniques complement carving by enabling the creation of unique forms. They include methods like mold-making, where a carved wax model is used to create a negative impression in a material like silicone or rubber. This allows for the production of multiple copies, ideal for jewelry making and small-batch production. Other techniques focus on direct modeling, using heated wax to shape and modify designs, offering artists greater flexibility and the ability to achieve complex forms suitable for modern jewelry casting.