Mastering Jewelry Casting: Defect Prevention and Detection Techniques
Jewelry casting involves various techniques, each presenting unique challenges like air bubbles, mol…….
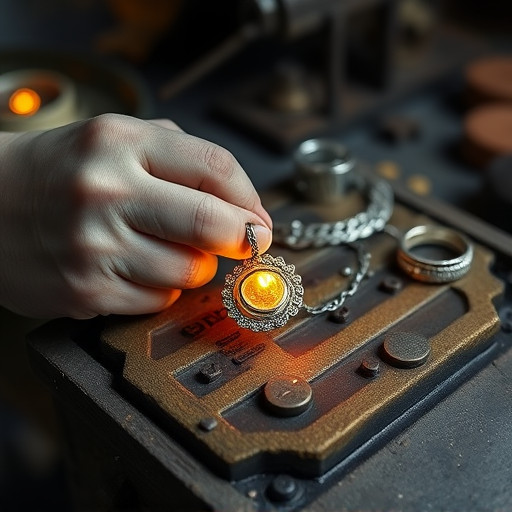
Jewelry casting involves various techniques, each presenting unique challenges like air bubbles, mold imperfections, and metal flow issues. Defects significantly impact product quality and aesthetics, arising from factors such as gas trapping, incomplete metal flow, and rapid cooling. Skilled jewelers use advanced techniques, equipment, and strict quality control to prevent these defects, ensuring structural integrity and high-quality results. Detecting flaws early through visual inspection and non-destructive testing is crucial; this ensures the creation of exquisite, defect-free jewelry pieces.
In the intricate world of jewelry crafting, understanding the nuances of casting processes is paramount. This article delves into the complexities of jewelry casting, exploring common defects, their causes, and effective prevention strategies. From detection methods to the impact on quality and value, we uncover industry secrets. Furthermore, advanced techniques and best practices are highlighted, providing a comprehensive guide for artisans aiming to minimize defect occurrence and ensure superior jewelry production. Discover the art and science behind flawless jewelry casting.
- Understanding Jewelry Casting Processes
- Common Types of Casting Defects
- Causes and Prevention Strategies
- Detection Methods for Casting Flaws
Understanding Jewelry Casting Processes
Jewelry casting is a complex art that involves creating intricate designs by pouring molten metal into a mold, which later hardens to form the desired shape. This process is at the heart of many jewelry-making techniques, from traditional hand-casting to modern machine-based methods. By understanding these casting processes, artisans and manufacturers can better address potential defects that may arise during production.
Each jewelry casting technique has its unique characteristics and challenges. For instance, lost-wax casting involves creating a wax model, which is then replicated in a mold using ceramic or metal materials. The molten metal is poured into this mold, and upon cooling, the wax core is removed, leaving a hollow form ready for stone settings. Defects like air bubbles, mold imperfections, or improper metal flow can impact the final product’s quality. Knowing these potential issues allows for precise control during casting, ensuring consistent and high-quality jewelry pieces.
Common Types of Casting Defects
In jewelry casting, various defects can arise during the process, each with its own unique impact on the final product. Common types include air bubbles, which form when gases become trapped within the molten metal; porosity, resulting from incomplete metal flow or rapid cooling; and misalignment, occurring when components shift during the casting process. These defects not only affect the aesthetic appeal of the jewelry but can also compromise its structural integrity.
Additionally, shrinkage cracks often develop due to the natural contraction of metal as it cools, while cold shut defects happen when the casting surface solidifies before the underlying layers, leading to weak points in the design. Skilled jewelers employ various techniques and specialized equipment to mitigate these issues, ensuring high-quality, defect-free pieces that meet the demands of modern jewelry production.
Causes and Prevention Strategies
Casting defects in jewelry production can arise from various factors, each requiring specific attention during the intricate process of jewelry casting. One of the primary causes is the use of impure or substandard materials, which can introduce impurities into the melt, leading to porosity and other structural issues in the final cast piece. Another common culprit is inadequate preparation of the mold, such as surface imperfections or improper release agents, resulting in flaws like air bubbles, misaligned walls, or incomplete filling.
To mitigate these defects, a robust prevention strategy involves meticulous material quality control, ensuring only high-purity metals and approved additives are used. Regular cleaning and maintenance of casting equipment, including mold preparation, are vital. This includes utilizing appropriate release agents to facilitate easy mold removal while maintaining the integrity of the cast shape. Additionally, implementing strict safety protocols and operator training can significantly reduce human error, which is a leading cause of casting defects.
Detection Methods for Casting Flaws
In the meticulous world of jewelry casting, detecting flaws is a critical step in ensuring the final product’s quality and beauty. Skilled artisans employ various advanced methods to identify even the subtlest imperfections that may arise during the casting process. One common technique involves visual inspection under magnified conditions, allowing for the detection of surface defects like air bubbles, metal shifts, or mold imperfections. This initial screening is crucial in jewelry casting, as it can catch issues early in the production line.
For more detailed analysis, non-destructive testing (NDT) methods are employed. These include ultrasonic testing, which uses high-frequency sound waves to detect internal flaws, and eddy current testing, that utilises electromagnetic induction to uncover surface and subsurface defects. Such sophisticated NDT techniques ensure that any casting flaws, such as cracks or porosity, are identified before the jewelry is further processed or set with gems, guaranteeing the creation of exquisite, defect-free pieces.