Mastering Jewelry Casting: A Guide for Small Businesses
Jewelry casting is a critical process for small businesses in the artisan and fine jewelry sectors,…….
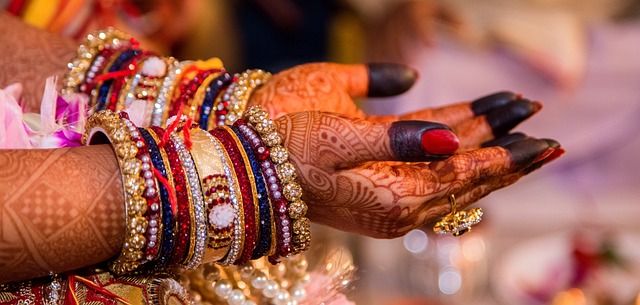
Jewelry casting is a critical process for small businesses in the artisan and fine jewelry sectors, allowing for the precise production of intricate designs with consistent quality. The casting process begins with crafting a detailed wax pattern that captures the design's essence, which is then encapsulated in a mold with investment material to maintain the integrity of the final piece. Once the investment sets, the wax is removed, and the mold is ready for molten metal to be poured in, replicating the design in its raw form. After cooling, the investment material is removed, and the jewelry undergoes cleaning, refinement, and finishing to achieve a polished, final product. Mastery of casting, including alloy selection and mold preparation, is essential for delivering high-quality jewelry that can compete in the marketplace. Small businesses benefit from this technique by creating unique pieces that rival mass-produced goods, with materials like silver, gold, and platinum commonly used due to their aesthetic appeal and durability. The process also accommodates sustainable materials, reflecting a growing trend towards environmental responsibility. Investment casting, in particular, is highlighted for its ability to produce complex designs with precision and consistency, making it suitable for both luxury and mass-market jewelry.
Exploring the intricacies of jewelry casting opens a gateway for small businesses to elevate their craft and expand their market reach. This comprehensive guide demystifies the casting process, essential equipment, and quality control measures necessary for flawless jewelry creation. From understanding the basics to mastering the art of mold making and selecting the right materials, each section provides clarity and practical advice. Small business owners will learn how to set up a safe and compliant casting operation, refine their techniques for consistently high-quality pieces, and effectively market their unique designs. Whether you’re new to jewelry casting or looking to perfect your craft, this article is designed to guide you through each step, ensuring your small business shines in the competitive jewelry market.
- Understanding the Basics of Jewelry Casting for Small Businesses
- – The Casting Process Explained
- – Materials and Alloys Commonly Used in Jewelry Casting
Understanding the Basics of Jewelry Casting for Small Businesses
In the realm of jewelry making, casting is a pivotal process that enables small businesses to create intricate and detailed pieces efficiently. Jewelry casting involves pouring molten metal into a mold to form the desired shape and size. For small-scale enterprises, mastering this technique can be a game-changer, allowing for the replication of designs with precision and consistency. The process begins with creating a pattern or model that captures all the finer details of the design. This pattern is then copied into a mold, which is carefully prepared to ensure it reflects the intricacies of the original model. Once the mold is set, investment material is applied to it, creating a barrier between the molten metal and the mold during the casting process. The actual casting involves melting the chosen metal alloy and pouring it into the prepared mold, where it solidifies into the desired shape. After the metal has cooled and hardened, the investment is removed, revealing the raw casting. Post-casting, the piece undergoes cleaning, refining, and finishing to achieve the polished and exquisite final product that customers desire. Understanding the nuances of jewelry casting, from choosing the appropriate alloy for durability and wearability to perfecting the mold-making technique, is crucial for small businesses aiming to produce high-quality jewelry. By adhering to best practices in each stage of the process, small jewelry businesses can ensure their castings meet the highest standards, setting them apart in a competitive market.
Jewelry casting is a critical process for small businesses in the jewelry-making industry, allowing artisans to translate their intricate designs into tangible pieces. This process involves creating a mold from a wax or resin model of the desired piece and then filling it with molten metal, typically sterling silver, gold, or other precious metals. The precision and detail achieved through casting enable small businesses to offer unique, high-quality jewelry that can compete with mass-produced items.
Choosing the right materials and equipment for jewelry casting is paramount for success. Small businesses must consider the type of metal they will use and the kind of investment casting process suitable for their operations. It’s essential to select a reliable foundry, as they will be instrumental in producing the final product. Additionally, understanding the various alloys and their properties can significantly impact the durability and luster of the finished jewelry. By mastering the art of casting, small businesses can craft pieces that are both beautiful and durable, satisfying the discerning tastes of contemporary consumers while maintaining the integrity of traditional jewelry-making techniques.
– The Casting Process Explained
Jewelry casting is a precise and intricate process that small businesses often utilize to create intricate and detailed pieces. This method involves pouring molten metal into a mold to form the desired shape. The process begins with creating a wax model that accurately represents the final piece of jewelry. This model is then attached to a sprue, which serves as a channel for the molten metal to enter during casting. The assembly is dipped repeatedly in a liquid slurry, building up layers of investment material around the wax. Once the investment material hardens, the wax is melted away, leaving a cavity shaped exactly like the jewelry item.
The actual casting process requires careful control of temperature and timing to ensure the metal fills the mold correctly without trapping any bubbles that could mar the final product. Silver, gold, platinum, and various other metals used in jewelry can be cast using this method. After the metal has solidified, the mold is broken away, and the rough casting is removed. The piece then undergoes a series of cleanup processes where excess material is filed and polished to achieve the fine finish characteristic of high-quality jewelry. This meticulous casting process allows small businesses to produce unique and complex designs that might be challenging or impossible to create by other means, making it a cornerstone of modern jewelry manufacturing.
– Materials and Alloys Commonly Used in Jewelry Casting
In the realm of jewelry casting, a variety of materials and alloys are employed to create pieces that are both aesthetically pleasing and durable. Silver is a popular choice due to its affordability and attractive luster. It often comes in different finenesses like sterling silver, which is 92.5% pure silver combined with other metals for strength. Gold is another sought-after material, with its yellow hue being a symbol of wealth and status. Gold alloys are categorized by karat value, with 24k being pure gold, while lower karats (18k, 14k) are mixed with other metals like copper or nickel to enhance durability. Additionally, base metals such as brass and bronze are used for more affordable pieces, and these can be coated with a thin layer of gold or silver through a process known as electroplating to mimic the appearance of higher-value metals. For those looking for sustainable options, recycled materials and eco-friendly alloys are gaining popularity, reflecting a growing trend towards environmental responsibility in jewelry production.
When it comes to casting processes, each material requires specific techniques to ensure the best results. Investment casting is a common method in jewelry casting, where a wax model of the desired piece is created, covered with a refractory material, and then heated until the wax burns away, leaving a mold that can be filled with molten metal. This technique allows for intricate details and consistent results, making it suitable for both high-end and mass-produced jewelry items. The choice of alloy and casting method is crucial for small businesses to achieve the desired quality and financial feasibility in their products, as well as to comply with consumer preferences and market trends.