Mastering Jewelry Casting: A Deep Dive into Artisan Techniques and Traditions
Jewelry casting is a traditional yet precise craft essential to creating fine jewelry. This meticul…….
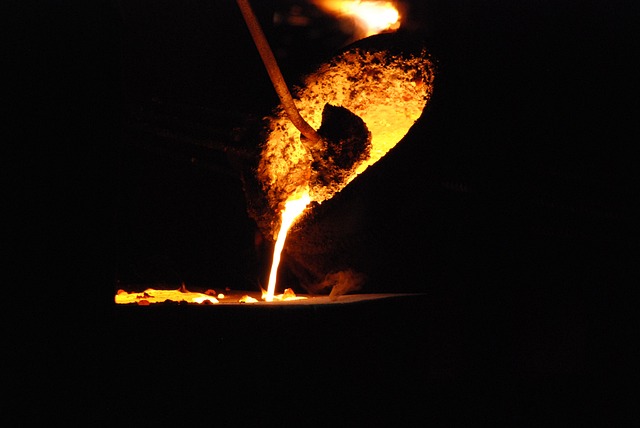
Jewelry casting is a traditional yet precise craft essential to creating fine jewelry. This meticulous process involves sculpting an exact wax model of the desired piece using lost-wax casting techniques, which is then attached to a sprue for metal flow management. The wax model is later enveloped in a silica sand and binding agent mixture for investment casting, ensuring every design detail is captured. Once invested, the wax is melted away, leaving a cavity for the molten precious metal—like silver or gold—to fill. Artisans carefully control the temperature of the furnace to pour the metal at the optimal state, avoiding defects. After cooling, the metal casting is extracted and undergoes detailed cleaning, finishing, and polishing, often including stone setting. This process showcases a blend of ancient artistry with modern precision, as artisans in jewelry casting workshops uphold tradition while adopting innovative techniques, ensuring the craft remains both culturally rich and technologically advanced. The result is a piece of wearable art that embodies the skill, dedication, and mastery of the artisan.
Embark on a journey into the heart of artisanal craftsmanship with our exploration of jewelry casting, a meticulous process that fuses tradition with modern innovation. This article delves into the intricate world of artisan workshops where master crafters breathe life into precious metals and gems. From the initial stages of wax carving to the final touches that reveal a piece’s luster, we uncover the steps involved in jewelry casting. Join us as we examine the tools and techniques that define this timeless art form, and consider how the interplay between age-old practices and contemporary methods shapes the future of jewelry design.
- Understanding the Art of Jewelry Casting: A Glimpse into Artisan Workshops
- The Process of Jewelry Casting: From Wax Mold to Finished Piece
- Mastering the Craft: Tools and Techniques Used in Jewelry Casting
- The Significance of Tradition and Innovation in Contemporary Jewelry Casting Artisan Workshops
Understanding the Art of Jewelry Casting: A Glimpse into Artisan Workshops
Jewelry casting is a meticulous art form that resides within the realm of fine jewelry fabrication, practiced by skilled artisans in specialized workshops. The process begins with the creation of a model or mold from wax, which accurately represents the desired final piece. This stage is critical as it dictates the precision and intricacy of the final casting. Artisans carefully sculpt each detail, ensuring that every curve and facet is faithfully replicated. Once the wax model is complete, it undergoes a spruing process, where additional wax structures are attached to facilitate the flow of molten metal and create a clean separation for each piece after casting.
The actual casting process involves melting the chosen metal alloy to a precise temperature and then pouring it into the prepared wax mold. As the metal cools and solidifies within the mold, it takes on the exact form of the wax original. After cooling, the metal casting is then carefully removed from the mold, leaving behind a detailed replica of the initial wax model. The artisans meticulously clean and finish the piece, filing down any rough edges, and applying various surface treatments to achieve the desired luster and texture. This labor-intensive process requires a deep understanding of materials, heat control, and precise craftsmanship, all of which are honed through years of dedicated practice in artisan workshops. The resulting jewelry pieces embody the artisan’s skill, creativity, and attention to detail, making each casting a unique testament to the craftsperson’s expertise in jewelry casting.
The Process of Jewelry Casting: From Wax Mold to Finished Piece
Jewelry casting is an intricate process that transforms artists’ visions into tangible, wearable artifacts. This craft involves a series of precise steps that begin with the creation of a wax model, which accurately represents the desired jewelry piece. Artisans skillfully sculpt this model using techniques such as lost-wax casting, a method as old as civilization itself yet still relevant in contemporary jewelry making. The wax model is then attached to a sprue, a thin canal that will later facilitate the flow of molten metal, ensuring each piece receives the necessary material to take shape.
Once the wax model is prepared, it undergoes a process called investment. This involves coating the wax with a slurry of silica sand and a binding agent to form a hard, durable mold. The mold captures every intricate detail of the original wax design, allowing for complex patterns and textures to be perfectly replicated in metal. After the investment dries and sets, the workshop heats a furnace to a high temperature, melting the desired metal—often silver, gold, or their alloys—into a liquid state. The molten metal is then carefully poured into the mold, filling every crevice where the wax once was. Upon cooling, the metal takes the form of the jewelry piece, exact in its detail and ready for final finishing. Artisans remove the metal casting from the mold, trim off excess material, and meticulously file, sand, and polish each piece to a high sheen, readying it for inspection and, ultimately, for its new owner to cherish and adorn.
Mastering the Craft: Tools and Techniques Used in Jewelry Casting
Within the specialized domain of jewelry casting, artisans harness a symphony of techniques and tools to transform intricate designs into tangible adornments. The process commences with the creation of a precise model or mold from wax or other modeling materials, which accurately represents the intended piece of jewelry. This step is pivotal as it directly influences the final product’s detail and quality. Artisans meticulously sculpt each facet and curve to ensure the cast item replicates the original design with fidelity.
Once the model is complete, it is prepared for casting. The artisan chooses a material for casting—commonly silver, gold, or base metal alloys—and employs a flask and investment material to encapsulate the wax model, forming a durable mold. This mold is then heated in a specialized furnace until the wax melts away, leaving an empty cavity that will soon be filled with molten metal. The precision of this process is paramount; it requires a delicate balance of temperature control and timing to ensure the metal fills the mold without defects. After casting, the piece undergoes a series of post-casting treatments, including cleaning, finishing, and sometimes setting with gemstones, to achieve the luster and detail that define handcrafted jewelry. Mastery of these steps is essential for artisans who strive to produce jewelry castings of superior quality and beauty.
The Significance of Tradition and Innovation in Contemporary Jewelry Casting Artisan Workshops
Craftsmanship in jewelry casting has long been a blend of time-honored techniques and contemporary advancements. Artisan workshops across the globe continue to uphold traditional methods, which are integral to preserving the artistry and history inherent in each piece. These traditions, from wax carving to investment casting, have been passed down through generations, ensuring that each creation carries with it a narrative of skill and cultural heritage. In this context, innovation complements tradition rather than overshadows it. Technological enhancements in jewelry casting processes, such as the use of digital modeling and precise temperature controls in furnaces, allow artisans to expand their creative boundaries while maintaining the integrity of the craft. This fusion fosters an environment where artisans can push the boundaries of design, exploring new forms and materials, all while honoring the foundational skills that have defined the field for centuries. The significance of this dual approach is evident in the way it bridges past and future, allowing jewelry casting to remain a vibrant and evolving form of artistic expression. Artisan workshops thus stand as bastions of tradition, with an innovative edge that propels the art forward into contemporary relevance.