Mastering Jewelry Casting: A Comprehensive Guide to Wax Carving Techniques
The art of wax carving is an essential skill in the jewelry casting process, serving as the initial …….
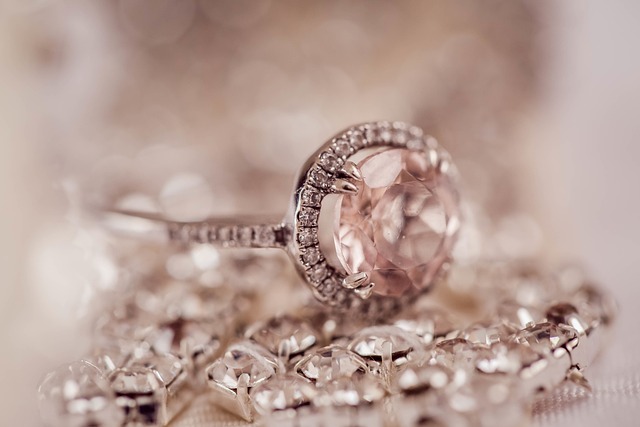
The art of wax carving is an essential skill in the jewelry casting process, serving as the initial step to create intricate and precise metal jewelry pieces with aesthetic finesse. This traditional technique involves hand-sculpting a detailed wax model that accurately represents the intended final piece. Carvers choose from soft or hard modeling waxes based on the design's complexity and their expertise; soft wax is ideal for delicate, complex designs, while hard wax suits larger, more substantial pieces. The carver uses specialized instruments to craft each aspect of the wax model, ensuring the final product is an exact miniature of the jewelry that will be cast. This wax model then undergoes the investment process, where it's coated with layers of liquid silica or similar materials to create a durable mold. Molten metal is subsequently poured into this mold, replicating every detail as it solidifies. The precision of the wax carving directly affects the quality and integrity of the final cast jewelry piece, making wax carving a linchpin in the high-quality production of fine jewelry through casting methods. This process also includes attaching a sprue for metal flow and preparing the model with investment materials, which are critical for maintaining the design's fidelity during the transition from wax to metal. Wax carving's role is indispensable in ensuring that complex patterns like filigree and granulation are perfectly replicated, underscoring its significance in the jewelry casting domain.
Discover the intricate art of jewelry casting through wax carving, a meticulous process that transforms intricate designs into wearable masterpieces. This article delves into the nuances of wax carving techniques, offering an in-depth exploration of the essential tools and materials required to excel in this craft. From foundational principles to advanced pattern creation, we guide you through each step, ensuring precision and consistency in your jewelry casting endeavors. Join us as we unveil the secrets behind breathtaking jewelry designs, enhancing your skills for exceptional outcomes.
- Mastering the Art of Wax Carving for Jewelry Casting: An Overview of Techniques and Tools
- The Fundamentals of Wax Carving: Materials, Models, and Design Considerations
Mastering the Art of Wax Carving for Jewelry Casting: An Overview of Techniques and Tools
Mastery in wax carving is a cornerstone for successful jewelry casting, as it lays the foundation for intricate designs to be translated into metal pieces with precision and elegance. Wax carving, also known as model making or investment casting, involves shaping a wax model that accurately represents the desired final piece of jewelry. The process commences with selecting appropriate tools and materials; carvers often choose between soft and hard wax depending on the complexity of the design and their proficiency level. Soft wax is malleable and suitable for detailed work, while hard wax provides greater stability for larger or more robust pieces.
To sculpt the wax model, a range of specialized instruments such as chisels, pin-tools, and needle files are employed. The carver meticulously hand-sculpts each facet, contour, and detail with these tools to replicate the jewelry’s intended appearance in miniature form. The precision of wax carving ensures that once the wax model is completed, it can be used to create a mold for casting. This step involves dipping the wax model into successive layers of liquid silica or other refractory materials, which harden to form a durable and precise mold. Subsequently, molten metal is poured into this mold, filling every detail as it solidifies into the final piece of jewelry. The skillful carver’s attention to detail in the wax model directly influences the quality and integrity of the cast piece, making the art of wax carving indispensable in the jewelry casting process.
Wax carving is an intricate and time-honored technique in the field of jewelry casting, allowing artisans to create detailed and complex designs with precision. The process commences with selecting the appropriate type of wax; typically, modeling wax is preferred due to its malleability and ease of detailing. Artisans skillfully sculpt the wax to mimic the desired shapes and intricate patterns of the final piece of jewelry. This craftsmanship is crucial for intricate details like filigree or granulation, which are challenging to replicate in metal.
Once the wax model is complete, it undergoes a series of preparatory steps before casting. These include attaching the model to a sprue, which serves as a conduit for molten metal during the pouring process. The attachment point, known as the investment or flask, surrounds the wax with plaster or resin material that will later be broken away to reveal the metal piece. This investment must be meticulously mixed and applied to ensure a durable and uniform mold; otherwise, it can lead to defects in the final casting. After the mold hardens, it is heated to burn out the wax, leaving an empty cavity that will be filled with molten metal. The precision of the wax carving directly translates to the quality and detail of the finished jewelry piece, making it a vital step in the jewelry casting process.
The Fundamentals of Wax Carving: Materials, Models, and Design Considerations
In the realm of fine jewelry creation, wax carving stands as a pivotal technique within the jewelry casting process. This intricate craft involves shaping a wax material into the desired design, which later serves as the mold for metal casting. The choice of wax is critical; traditional beeswax and paraffin are popular due to their malleability and ease of manipulation. These materials must be high-quality to ensure that the finished piece maintains its integrity during the investment process and subsequent metal casting.
The artisan begins by warming the wax to a pliable state, then manually or with the aid of tools such as carving knives, drills, and dental tools, sculpts the piece. The model emerges layer by layer, with attention given to every facet, curve, and detail that will later translate into the metal form. Design considerations are paramount; the complexity of the design affects the wax carving process, influencing the amount of time required and the intricacy of the tools needed. A well-crafted wax model not only accurately represents the final jewelry piece but also facilitates a smoother transition from concept to tangible object. The precision of wax carving ensures that when the metal is cast, it closely resembles the artist’s original vision, making it an indispensable step in the jewelry casting process.
Wax carving is an intricate and precise technique used in the field of jewelry casting, playing a pivotal role in creating intricate and detailed jewelry pieces. This traditional art form involves sculpting wax into the desired shape, which serves as a template for the final metal piece. Skilled artisans manipulate heated wax to carve out complex patterns, designs, and structures that are later replicated in metal through casting processes such as lost-wax casting. The precision of wax carving ensures that the minutiae of the design are accurately captured, resulting in high-quality jewelry with a smooth and polished finish. The consistency and flexibility of wax allow for easy modifications during the design process, enabling artisans to make adjustments without the risk of damaging the mold as would be the case with more rigid materials. This adaptability is particularly advantageous when creating unique, custom pieces that require a high level of detail and craftsmanship.
The wax carving technique for jewelry casting involves several stages, each crucial to achieving the best results. The artisan begins by sketching the design on a wax base, which is then heated until pliable. Using specialized tools, they sculpt the wax into the three-dimensional form, incorporating every detail of the future piece of jewelry. Once the carving is complete, the wax model undergoes a series of preparatory steps before casting. These include attaching additional wax pieces to create a sprue system for mold filling and attachment points for post-casting cleaning processes. The resulting wax tree, with its complex network of branches and connection points, is then invested in a refractory material, ready for the molten metal to be poured in, capturing every nuance of the original wax carving. This investment phase is critical as it ensures that the final metal piece accurately reflects the artist’s vision. The skillful integration of wax carving techniques in jewelry casting not only enhances the aesthetic appeal but also guarantees the structural integrity and durability of the finished piece.