Mastering Jewelry Casting: A Comprehensive Guide to Techniques and Materials
Jewelry casting is a meticulous process central to the creation of fine jewelry, utilizing techniqu…….
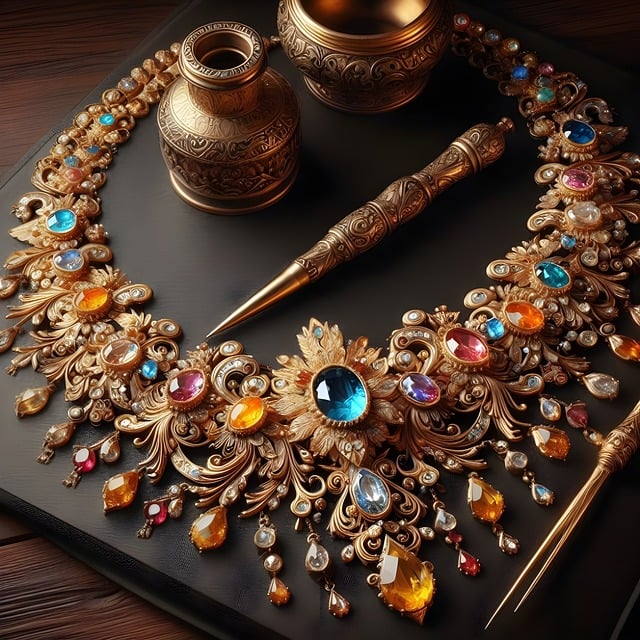
Jewelry casting is a meticulous process central to the creation of fine jewelry, utilizing techniques like lost-wax casting and investment molding to transform intricate designs into wearable art. The process begins with crafting a 'tree' model in wax or via 3D printing, which later splits into individual castings within a refractory mold chosen for its compatibility with the metal and desired finish. The mold is then covered with a casting investment—a mix of plaster and resin that hardens to protect the design during casting. In the lost-wax technique, the wax model is removed, leaving a cavity filled with molten metal, replicating the original design precisely. After cooling, the investment is removed, and the raw casting undergoes cleaning, finishing, and stone setting to achieve its final polished state. The entire process showcases a blend of artistry and scientific precision, resulting in high-quality jewelry that emphasizes intricate details and durability. The choice between lost-wax and investment molding techniques is crucial, depending on whether the focus is on complexity or efficiency. Jewelry casting involves working with precious metals like gold (in different karats), silver, and platinum, each chosen for specific properties and suitability in various designs. Alloys are often added to precious metals to enhance strength and appearance, while base metal alloys like sterling silver and brass provide economical options for mass production. The jewelry casting industry has seen significant advancements from ancient lost-wax techniques to modern precision investment casting, expanding creative potential and enabling large-scale production without sacrificing quality or detail. This field remains dynamic, with ongoing technological development and artistic expression driving innovation in fine jewelry creation. Keywords: jewelry casting, lost-wax technique, fine jewelry, intricate details, precision casting, precious metals, alloys, investment molding, modern advancements.
Explore the intricate art and science of jewelry casting, a technique integral to modern-day jewelry design. This article delves into the multifaceted process, shedding light on the various materials and alloys that form the foundation of this craft. Witness the transformation over time as we trace the evolution of casting methods and examine the critical role of wax models in bringing intricate designs to life. Discover the nuances of pattern making, the meticulous steps of the lost-wax casting method, and the post-casting techniques that yield flawless pieces. Investigate cutting-edge technologies and innovations shaping the industry’s future, while also considering safety and environmental concerns. Through a case study, we’ll explore a successful jewelry casting project, understand the business aspects from craft to commerce, and offer insights on selecting professional jewelers. Finally, we’ll address common queries about jewelry casting, ensuring you have a comprehensive understanding of this exquisite craft.
- Understanding the Jewelry Casting Process
- Materials and Alloys Commonly Used in Jewelry Casting
- The Evolution of Jewelry Casting Techniques
- Types of Molds in Jewelry Casting
Understanding the Jewelry Casting Process
Jewelry casting is a complex yet pivotal process in the fine jewelry industry, allowing artisans to transform intricate designs into tangible pieces of wearable art. The process begins with creating a mold from a model of the desired piece of jewelry, typically sculpted from wax or crafted using rapid prototyping techniques such as 3D printing. This model, known as a ‘tree,’ holds several individual castings that branch off a main structure, is then coated with a refractory material to form the mold. The choice of material for the mold depends on various factors including the metal being used and the desired finish of the final product.
Once the mold is prepared, it is heated in a casting investment, a mixture of plaster and resin that forms a hardened shell around the mold. This step is crucial as it ensures the integrity of the cast during the melting process. Molten metal is then introduced into the mold through a technique known as ‘lost-wax casting,’ where the wax tree is heated until it burns out, leaving a cavity that the metal fills. The metal solidifies in the exact shape as the original wax model, resulting in a detailed and precise replica. After cooling, the investment is removed to reveal the raw casting. Post-casting processes such as cleaning, finishing, and setting with gemstones follow, transforming the raw cast into the exquisite, final jewelry piece ready for discerning customers. This meticulous process of jewelry casting allows for high precision, intricate details, and consistent quality that are hallmarks of fine jewelry.
Materials and Alloys Commonly Used in Jewelry Casting
Jewelry casting is an intricate process that requires precise control and a deep understanding of materials and alloys to achieve high-quality pieces. Among the most common materials employed in jewelry casting are precious metals such as gold, silver, and platinum. Each of these metals has unique properties that make them suitable for various jewelry designs. Gold, available in 14K, 18K, and 22K variations, is a favorite for its durability and luster; it often contains alloys like copper, nickel, zinc, and palladium to enhance its strength and reduce wear. Silver, typically combined with alloys such as germination or nickel, offers a cost-effective alternative while maintaining an elegant appearance. Platinum, known for its density and purity, is often mixed with iridium, cobalt, or ruthenium to refine its malleability and ensure it can be cast into intricate designs without losing its luster or integrity.
In addition to these precious metals, base metal alloys such as sterling silver and various brass alloys are also used in jewelry casting. Sterling silver is an alloy of 92.5% pure silver with other metals like copper to increase its hardness and durability. Brass alloys, composed of copper and zinc, offer a more affordable option for mass-produced jewelry. These materials are chosen not only for their cost-effectiveness but also for their ease of casting and the ability to achieve complex shapes and details that can be difficult to obtain with precious metals alone. The choice of material and alloy in jewelry casting is critical, as it determines the final appearance, durability, and value of the finished piece.
The Evolution of Jewelry Casting Techniques
The art and craft of jewelry casting have undergone significant transformations over centuries, reflecting advancements in technology and materials. In ancient times, cire-perdue, or lost-wax casting, was already a revered technique, allowing artisans to create intricate designs with precision and detail that were nearly identical to the original wax models. Over time, this method became more sophisticated, with improvements in mold making, alloy composition, and melting processes enhancing the quality and durability of cast pieces.
With the advent of modern technology, jewelry casting has experienced a renaissance. The introduction of precision investment casting techniques enabled the mass production of jewelry while maintaining high standards of quality and intricacy. This method, also known as the ‘lost-wax’ process, involves creating a mold from an investment material that is a plaster or resin mixture. Once the metal is poured into the mold, it takes the form of the jewelry design. The evolution of casting techniques has not only increased efficiency and consistency but has also expanded the possibilities for designers to innovate with new alloys, designs, and textures, making jewelry casting a dynamic field that continues to evolve with technological advancements.
Types of Molds in Jewelry Casting
Jewelry casting is a critical process in the creation of intricate and detailed pieces, where molds play an integral role. In jewelry casting, molds can be categorized into two primary types: investment and lost-wax methods. The investment mold technique involves creating a master model that is then covered in a refractory material called investment. Once the investment hardens, it forms a negative impression of the original model. This mold is then used to cast the metal, which fills the cavity, resulting in a replica of the original design with fine details preserved.
The lost-wax process, another common method in jewelry casting, uses a wax replica of the desired piece. This wax model is coated with a refractory material to form a protective mold. After the wax and excess slurry are removed, leaving behind an empty cavity, the mold is heated to burn out the wax, leaving only the refractory mold. Molten metal is then poured into this cavity. Both methods require precise technique and careful handling of materials to ensure the integrity and quality of the final jewelry piece. Each type of mold offers distinct advantages; investment molds are excellent for complex designs with intricate details, while lost-wax molds are suitable for larger production runs due to their efficiency and scalability. Understanding the nuances of each mold type is crucial for artisans in the jewelry industry to produce high-quality, durable, and beautiful pieces that meet the exacting standards of modern consumers.