Mastering Excellence: Quality Control Essentials in Jewelry Casting Processes
Jewelry casting is a meticulous process that marries artistry with precision to create exquisite pie…….
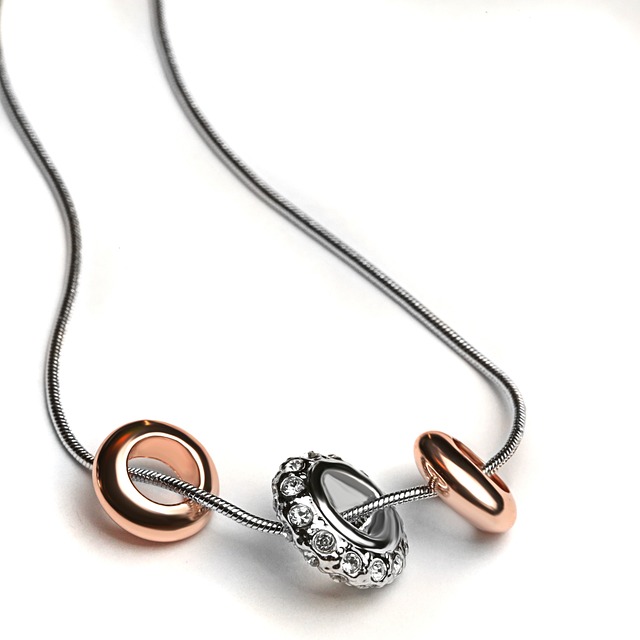
Jewelry casting is a meticulous process that marries artistry with precision to create exquisite pieces. It involves crafting a detailed wax or resin model that is used to produce an exact mold for casting metal. The choice of materials—both for the mold and the metal alloy—is critical, as it affects the jewelry's aesthetic appeal, durability, and luster. Artisans ensure meticulous attention to detail during the modeling phase to bring the designer's vision to life. Post-casting, the artisan performs necessary operations such as cleaning, finishing, and gemstone setting. Quality control is integral throughout the process, from the initial wax carving to the final polish, ensuring that the resulting jewelry meets and surpasses high industry standards for quality and craftsmanship. Innovations like CAD, 3D printing, NDT technologies including XRF and 3D scanning, spectrometry, and imaging systems are now employed to enhance efficiency and maintain high-quality standards in the jewelry casting process, setting superior pieces apart from others in the industry.
jewelry casting is an art form blending precision with traditional craftsmanship, a process integral to producing exquisite pieces that adorn both individuals and collections. This article delves into the nuances of quality control within this intricate field, highlighting its pivotal role in transforming intricate wax models into enduring metal masterpieces. From the initial selection of materials to the meticulous final inspections, we explore the critical steps ensuring each piece meets the highest standards. Furthermore, we examine advanced techniques and technology that elevate quality control, propelling the jewelry casting industry towards a future where excellence is not just pursued but consistently achieved.
- Understanding the Jewelry Casting Process: A Primer on Precision and Craftsmanship
- The Role of Quality Control in Jewelry Casting: Ensuring Excellence from Wax to Metal
- Key Steps in Quality Control for Jewelry Casting: From Material Selection to Final Inspection
- Advanced Techniques and Technology in Jewelry Casting: Innovations Driving Higher Standards in Quality Control
Understanding the Jewelry Casting Process: A Primer on Precision and Craftsmanship
The jewelry casting process is a delicate interplay of art and science, requiring precise execution to achieve high-quality results. At its core, this process involves creating a mold from a wax or resin model of the desired piece of jewelry, which is then filled with molten metal to form the final product. The accuracy of the mold is paramount; it must faithfully replicate every detail of the original model, ensuring that the cast item has the intended dimensions, surface finish, and design elements. Skilled artisans meticulously prepare the models, ensuring they are flawless and true to the designer’s vision before casting. The selection of materials for both the mold and the metal is critical; different alloys and materials lend themselves to various types of jewelry, affecting everything from durability to shine. After the metal cools and solidifies within the mold, a skilled caster removes the piece and performs secondary operations such as cleaning, finishing, and setting gemstones, if necessary. Throughout this process, quality control measures are integral; from the initial wax carving to the final polish, each step is scrutinized for imperfections. This commitment to precision and craftsmanship ensures that the end product not only meets but exceeds the high standards expected in fine jewelry casting. The consistent application of quality control protocols is what distinguishes exceptional jewelry from ordinary pieces, underscoring the importance of diligence at every stage of the casting process.
The Role of Quality Control in Jewelry Casting: Ensuring Excellence from Wax to Metal
Within the intricate process of jewelry casting, quality control plays a pivotal role in achieving the highest standards of excellence from the initial wax model to the final metal piece. The journey begins with precise pattern making, where artisans craft detailed wax molds that accurately represent the desired jewelry design. At this stage, quality control measures are implemented to ensure each wax pattern’s dimensions and details align with the design specifications. Any discrepancies are corrected before progressing to the casting process.
Once the wax models have been verified for accuracy, they undergo a loss of wax investment casting procedure. This critical step involves creating a mold from the wax patterns, which is then filled with molten metal under high heat. Quality control is paramount during this phase, as it influences the integrity and beauty of the final product. Meticulous oversight is required to monitor the casting process, ensuring that the metal perfectly fills the mold without defects such as air bubbles or incomplete fill. After casting, the metal pieces are carefully extracted, cleaned, and assessed for any imperfections that may have occurred during the pouring or solidification stages. The subsequent finishing processes, including cutting, polishing, and setting of gemstones, are guided by quality control standards to ensure the jewelry not only meets but exceeds the expectations of discerning clients. Throughout this entire process, from wax to metal, quality control is a non-negotiable cornerstone that guarantees the craftsmanship and longevity of each exquisite piece.
Key Steps in Quality Control for Jewelry Casting: From Material Selection to Final Inspection
In the realm of jewelry craftsmanship, jewelry casting is a meticulous process that demands stringent quality control measures to ensure the final pieces meet the highest standards. The journey from material selection to the final inspection is pivotal and involves several key steps. At the outset, the choice of materials—including metal alloys and any additional elements like gemstones—is critical. These materials must be sourced from reputable suppliers to ensure consistency and quality. Once the raw materials are in hand, the preparation process begins, where the purity and composition of the metal are verified. This is a decisive step as it directly affects the integrity of the cast and the longevity of the finished jewelry.
The casting process itself requires precise control over temperature and duration to facilitate proper molten metal flow into molds without creating defects such as air bubbles or cold shuts. After casting, the pieces undergo a series of cooling processes that must be carefully managed to avoid warping or distortion. Post-casting, the initial inspection assesses the external and internal structure of the cast jewelry, looking for any irregularities or imperfections. Subsequent stages involve polishing, setting gemstones, and final finishing, each requiring close attention to detail. Throughout these stages, quality control checks are conducted to ensure that the dimensions, weight, and appearance conform to design specifications. The final inspection is a comprehensive evaluation where jewelry pieces are assessed against stringent criteria, including structural integrity, aesthetic appeal, and safety standards. Only when all these quality control measures have been satisfactorily met does the jewelry casting process culminate in a product that upholds the esteemed reputation of the jeweler and delights the customer.
Advanced Techniques and Technology in Jewelry Casting: Innovations Driving Higher Standards in Quality Control
Precision and consistency are paramount in the realm of jewelry casting, where the finest details can differentiate high-quality pieces from their inferior counterparts. The integration of advanced techniques and technology has significantly elevated the standards of quality control within this meticulous craft. Modern casting processes such as lost-wax casting have been refined with computer-aided design (CAD) and 3D printing, allowing for intricate designs to be replicated with unparalleled accuracy. These digital advancements enable artisans to create precise models before casting, reducing the margin of error and ensuring that each cast piece aligns closely with its intended specifications.
Furthermore, non-destructive testing (NDT) methods like X-ray fluorescence (XRF) and 3D scanning have become indispensable tools in maintaining the integrity of jewelry pieces. These technologies enable thorough inspections to detect any inconsistencies or imperfections that could compromise quality. Advanced spectrometry and imaging systems allow for the precise measurement of gemstones and metal composition, ensuring that each piece meets the highest standards. The continuous integration of such sophisticated techniques and technology not only streamlines the casting process but also guarantees that the final jewelry products are of the utmost quality, reflecting a commitment to excellence in the industry.