Mastering Bespoke Jewelry Casting: A Comprehensive Guide
The section delves into the precision and expertise required in bespoke jewelry casting, a foundati…….
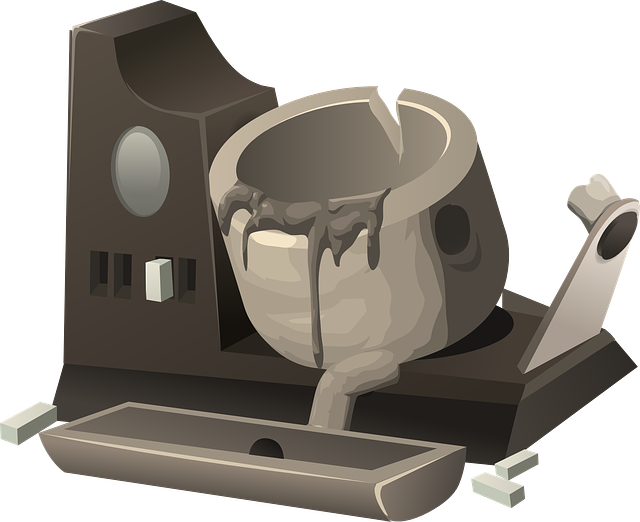
The section delves into the precision and expertise required in bespoke jewelry casting, a foundational process in high-end jewelry creation. It outlines how designers translate their visions into detailed wax models, which are then transformed into molds using either hand sculpting or digital technology. The casting process involves pouring molten metal into these molds, which have been coated with a ceramic slurry to form durable and precise molds. The choice of metal—such as 18k gold for its craftability, silver for its versatility, or platinum for its longevity and hypoallergenic properties—plays a crucial role in the piece's final look and durability. Post-casting, artisans meticulously clean, file, polish, and set stones to perfect each piece, ensuring that the jewelry not only reflects the wearer's personal style but also showcases the artisan's mastery of their craft. The article emphasizes that bespoke jewelry casting is a blend of traditional skills with modern technology, resulting in unique, high-quality pieces that embody the essence of bespoke design and craftsmanship.
Explore the intricate artistry behind bespoke jewelry casting, a process that transforms artistic visions into wearable masterpieces. This article delves into the nuanced techniques and precise craftsmanship involved in creating these timeless treasures. From selecting appropriate metals to meticulously crafting molds and applying post-casting finishes, we will unravel each step of this transformative journey, highlighting the importance of jewelry casting in bespoke design. Join us as we shed light on the details that make these pieces not just ornaments, but embodiments of creativity and skill.
- Understanding the Art of Jewelry Casting: From Concept to Creation
- The Precision of Jewelry Molds: Techniques for Crafting the Perfect Matrix
- Material Matters: Selecting and Working with Different Metals in Jewelry Casting
- The Finishing Touch: Post-Casting Processes for Bespoke Jewelry Masterpieces
Understanding the Art of Jewelry Casting: From Concept to Creation
Crafting bespoke jewelry is an art form that demands precision, creativity, and a deep understanding of the jewelry casting process. At the heart of this craft lies the technique of casting, which transforms wax models into intricate pieces of wearable art. Jewelry casting begins with the designer’s concept, which is meticulously sculpted in clay or modeled digitally to create a detailed wax pattern. This pattern serves as the blueprint for the final piece, capturing every nuance and detail that will define its beauty and uniqueness.
Once the wax pattern is complete, it is attached to a sprue, which acts as a conduit for molten metal during the casting process. The attachment of the sprue is crucial as it allows for the flow of metal into the mold without compromise to the design’s integrity. In the casting chamber, the wax pattern is enveloped in a ceramic slurry, building a durable and precise mold around the pattern. This mold hardens and is then heated to a high temperature, causing the wax to melt out, leaving a cavity perfectly shaped for the desired metal. Molten metal is then carefully poured into this cavity, filling it and eventually cooling into the jewelry piece’s future form. After the metal has solidified, the ceramic mold is removed, revealing the raw casting. From here, the piece undergoes further refinement through processes such as cleaning, filing, polishing, and setting with gemstones if required. Each stage of this intricate process requires a blend of technical skill and artistry to ensure the final creation meets the high standards expected in bespoke jewelry. The journey from concept to creation in jewelry casting is a testament to the dedication and craftsmanship that goes into each unique piece, making it an integral part of the luxury jewelry industry.
The Precision of Jewelry Molds: Techniques for Crafting the Perfect Matrix
Jewelry casting is a meticulous process at the heart of bespoke jewelry creation, where the precision of jewelry molds plays a pivotal role in crafting exquisite pieces. The artisanship involved in creating the perfect matrix for jewelry casting begins with the selection of materials for the mold. High-quality silicone or wax is often employed to generate a negative impression that captures the intricate details of the design with unparalleled accuracy. This initial step ensures that every contour and facet of the design is preserved in metal once the molten material fills the void left by the matrix.
The precision required for jewelry molds extends beyond the choice of material to the techniques used to construct them. Skilled artisans employ advanced modeling software to create a digital prototype of the piece, which is then printed in a resin that mimics the texture and form of the final product. This prototype serves as a guide for carving the jewelry mold, allowing for minute adjustments to be made before the actual casting process begins. The craftsman must ensure that every angle, curve, and surface is replicated with exactness in the matrix. Once the mold is complete, it is carefully placed within a casting machine where molten metal is poured to form the final piece. The result is a bespoke jewelry item that embodies the original design’s intent with remarkable fidelity, thanks to the precision of the jewelry mold and the meticulous techniques employed during the casting process.
Material Matters: Selecting and Working with Different Metals in Jewelry Casting
In the realm of bespoke jewelry creation, the choice of metal is a pivotal aspect of the design process, influencing both the piece’s aesthetic and its durability. Jewelry casting techniques demand metals with specific properties to ensure high-quality outcomes. Gold, for instance, comes in various karats, each offering different characteristics; 18k gold, with its higher purity, casts well but may require more skill to work with due to its softer nature. Silver, a popular choice for casting due to its affordability and malleability, provides a brilliant finish and is suitable for a wide range of designs. Alternatively, platinum is valued for its longevity and hypoallergenic qualities, making it an excellent option for those sensitive to other metals. Each metal brings its own set of challenges and benefits to the casting process, necessitating tailored approaches in terms of mold preparation, alloy selection, and post-casting finishing techniques. The artisan’s expertise in handling these diverse materials is crucial; they must understand the nuances of each metal to achieve the desired result, whether it be a lustrous gold pendant or an intricate silver brooch. Jewelry casting, therefore, is not merely a technical process but an interplay of material properties and skilled craftsmanship, resulting in unique, lasting pieces that reflect both the artisan’s expertise and the wearer’s personal style.
The Finishing Touch: Post-Casting Processes for Bespoke Jewelry Masterpieces
Jewelry casting is an integral part of the bespoke jewelry creation process, transforming molten metal into intricate forms that serve as the foundation for exquisite pieces. Once the initial casting is complete, the real artistry unfolds in the post-casting processes. These meticulous steps are where craftsmanship truly shines, elevating raw castings to the status of bespoke masterpieces.
Craftsmen employ a variety of techniques to refine the surface texture and enhance the details of each piece. The casting is carefully examined for imperfections; areas that are too thick or thin are corrected through skilled filing and adjustments. A masterful finish is achieved through a combination of hand-finishing and mechanical polishing, ensuring each facet captures light perfectly. Texturing and patina application can then add depth and character to the metalwork, creating a unique visual impact that sets bespoke jewelry apart. The application of precious stones, if required, is done with precision to complement the surrounding design, culminating in a piece that reflects the wearer’s individuality and the artisan’s expertise in jewelry casting.