Lost-Wax Casting: The Art and Science of Precision Jewelry
The lost-wax casting process is a fundamental and ancient jewelry casting technique that continues t…….
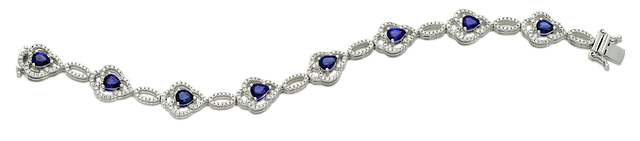
The lost-wax casting process is a fundamental and ancient jewelry casting technique that continues to be highly relevant in modern times. It involves crafting a detailed wax model that accurately represents the desired piece of jewelry, which is then encased in a refractory material to create a mold. After heating to remove the wax, the mold is filled with molten precious metal, such as gold or silver, which cools and solidifies into a replica of the original design. This method allows for intricate details and flawless surfaces, making it ideal for fine jewelry. Despite its origins in ancient civilizations like Mesoamerica and those in the Old World, lost-wax casting has evolved with modern technology, incorporating advancements such as 3D printing for precise wax models and enhanced pouring systems to improve casting quality. These innovations have made this technique more accessible, allowing a broader range of artisans to produce high-quality, detailed jewelry while maintaining its traditional craftsmanship legacy.
The art of jewelry casting, particularly the lost-wax casting process, stands as a pinnacle of craftsmanship that marries intricate design with precise execution. This article delves into the nuanced techniques behind this ancient form of artistry, offering insights from its historical origins to modern advancements in the field. We will guide you through the steps of the lost-wax casting technique, revealing how master jewelers craft exquisite pieces that capture the imagination and grace the adorned. Join us as we explore the timeless allure of this jewelry-making process and the challenges it presents to artisans striving for excellence in their craft.
- Unraveling the Intricacies of the Lost-wax Casting Process in Jewelry Making
- Historical Origins and Evolution of Lost-wax Casting in Jewelry Design
- Step-by-Step Guide to the Lost-wax Casting Technique for Crafting Fine Jewelry
- Mastering Lost-wax Casting: Tips, Challenges, and Innovations in Modern Jewelry Casting
Unraveling the Intricacies of the Lost-wax Casting Process in Jewelry Making
The lost-wax casting process, a pivotal technique in the jewelry-making realm, intricately combines precision and artistry to create intricate and detailed pieces. This ancient method, also known as investment casting, involves crafting an original model or wax mold that accurately represents the desired final piece of jewelry. The model is meticulously coated with a refractory material, which, upon hardening, forms a mold. The wax is then melted away, leaving behind an empty cavity that matches the jewelry design. Molten metal is subsequently poured into this cavity. As the metal cools and solidifies within the mold, it takes on the exact form of the original wax model. This technique allows for complex designs and detailed patterns that would be challenging, if not impossible, to achieve through other casting methods. The resulting pieces exhibit a level of detail and finish that is unattainable by many traditional jewelry-making techniques, making the lost-wax casting process a cornerstone in high-quality jewelry production.
The intricate nature of the lost-wax casting process requires a precise sequence of steps, each critical to achieving the high standards expected in fine jewelry. The preliminary phase involves designing and creating the initial wax model, which serves as the blueprint for the entire casting procedure. This model undergoes an exacting process where it is encased in a heated fluid to remove any imperfections, ensuring the final product’s surface will be flawless. Once the model is prepared, it is coated with a ceramic slurry that hardens into a durable mold. The wax is then removed, either by melting or through a technique known as ‘spruing,’ where additional wax structures called ‘gates’ and ‘risers’ are added to facilitate the metal flow and air bubble escape during casting. Finally, the molten metal, typically a precious alloy for jewelry applications, is poured into the mold cavity. The skillful execution of this process yields pieces with exceptional quality and detail, making lost-wax casting an essential technique in modern jewelry casting.
Historical Origins and Evolution of Lost-wax Casting in Jewelry Design
The lost-wax casting process, a technique integral to jewelry casting, boasts a storied history that spans millennia, with its origins tracing back to ancient civilizations. Artisans from Mesoamerica and the Old World, including ancient Egyptians, Indians, and Chinese, independently developed this intricate method, showcasing its global significance in jewelry design. The process, which involves creating a mold from wax that represents the desired object, has been refined over time, evolving from its rudimentary beginnings to a sophisticated art form. This ancient technique has left a profound mark on the evolution of jewelry design, enabling the creation of intricate and detailed pieces that were once thought impossible to craft by hand. Today, lost-wax casting remains an invaluable process in the jewelry industry, allowing for the production of complex designs with high precision and detail, ensuring its place as a cornerstone of jewelry casting techniques. The advancements in materials and technology have further enhanced this method, making it accessible to artisans and designers worldwide who continue to innovate within the bounds of this ancient craft.
Step-by-Step Guide to the Lost-wax Casting Technique for Crafting Fine Jewelry
The lost-wax casting technique is a meticulous process employed by artisans to craft intricate and exquisite fine jewelry. This ancient method, also known as investment casting, has been refined over centuries to produce pieces with high precision and detail. The journey of a wax model into a solid piece of jewelry begins with the design phase, where artisans create a detailed wax mold that accurately represents the desired final piece. Each element, from the smallest grain to the grandest ornament, is intricately shaped within this mold. Once complete, the wax model undergoes a series of preparatory steps. It is coated with a refractory material, which, upon heating, will form a durable and sturdy mold. This protective layer ensures that the delicate details of the wax are captured and preserved in metal.
The next stage involves melting the chosen metal, typically gold, silver, or a base metal alloy, to a precise temperature. The molten metal is then carefully poured into the investment mold, filling every crevice and taking the place of the original wax. As the metal cools and solidifies, it assumes the shape of the wax, which has since vaporized or been burned away. Post-casting, the jewelry piece requires cleaning and finishing, where artisans remove any excess material and meticulously smooth surfaces to achieve a flawless finish. Finally, the piece is polished to bring out its natural luster and brilliance, ready to adorn and captivate its future wearer. This labor-intensive process exemplifies the dedication and craftsmanship involved in jewelry casting, resulting in pieces that are both beautiful and enduring.
Mastering Lost-wax Casting: Tips, Challenges, and Innovations in Modern Jewelry Casting
Mastering the lost-wax casting process in jewelry making is a blend of traditional craftsmanship and modern innovation. This intricate technique, also known as investment casting, involves creating a mold from a wax model that accurately represents the desired piece of jewelry. The first step is to sculpt or model the jewelry in wax, capturing all the minute details that will translate into the final metal piece. This stage requires a deep understanding of design and the material properties of wax, which serves as both the pattern for the mold and the core around which the metal will solidify.
Once the wax model is complete, it undergoes a series of processes including coating with refractory material to form the investment, creating a ceramic shell that will become the mold. The flasks are then baked in a kiln to remove the wax, leaving behind an empty cavity shaped exactly like the original wax model. Molten metal is then introduced into this cavity; as it cools, it takes on the shape of the original design. This process requires precise control over temperature and material composition to ensure the integrity of the final product. The challenges inherent in lost-wax casting include maintaining consistency in the ceramic shell’s thickness and porosity, ensuring the accuracy of the wax model, and controlling the metal pour to avoid defects such as air pockets or misruns.
Innovations in jewelry casting technology have led to advancements that make the process more efficient and less prone to errors. Technological improvements in 3D printing have allowed jewelers to create detailed wax models directly from digital designs, reducing the time and skill traditionally required for hand-sculpting. Additionally, new investment materials and controlled pouring systems have improved the quality and repeatability of castings. These technological strides have democratized jewelry casting, making it accessible to a wider range of artisans and designers while preserving the intricate details and unique beauty that lost-wax casting is renowned for.