Jewelry Casting Face-off: Mastering Lost-wax vs. Revolutionizing with 3D Printing
Jewelry casting techniques, particularly lost-wax casting and 3D printing, are central to the creati…….
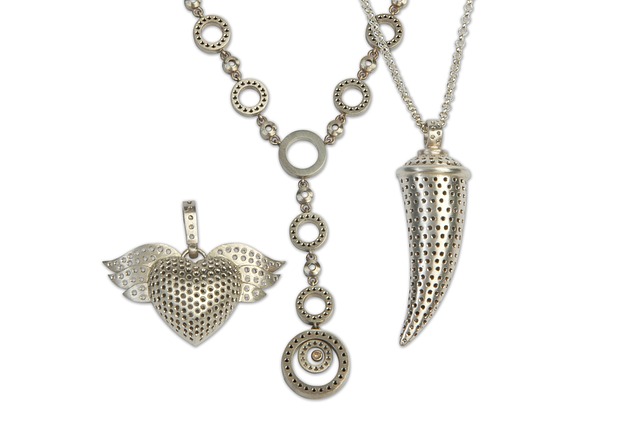
Jewelry casting techniques, particularly lost-wax casting and 3D printing, are central to the creation of intricate and detailed pieces in the fine jewelry industry. Lost-wax casting, with its deep historical roots, is valued for its ability to capture exquisite detail and provide artisanal charm. This ancient method involves sculpting a wax model, encasing it, and then casting metal into the resulting mold after the wax is removed. It has been used since at least 3700 BCE by civilizations like those of Mesopotamia and Egypt, experienced a revival during the Renaissance, and remains integral to traditional jewelry making today.
On the flip side, 3D printing, a modern innovation, has revolutionized jewelry design and production with its precision, efficiency, and versatility. It allows for rapid prototyping and is ideal for both custom and high-volume manufacturing. This method enables complex designs that were previously impossible to achieve, offers personalization, and supports sustainability and consumer-focused practices. Both lost-wax casting and 3D printing complement each other, pushing the boundaries of design and craftsmanship in the jewelry industry, offering superior detail and precision, and catering to diverse needs with high-quality and innovative pieces.
Explore the artistry and technology convergence in modern jewelry design through the lens of two pivotal casting techniques: lost-wax casting and 3D printing. This article delves into the rich history, intricate mechanics, and innovative potential of these methods, offering a comparative analysis that illuminates their respective roles in shaping the future of jewelry casting. Discover how each technique influences precision, detail, and personalization in the creation of exquisite pieces, and understand why the choice between lost-wax casting and 3D printing can significantly impact both the artistic outcome and the production process in the jewelry industry.
- Overview of Jewelry Casting Techniques: Lost-wax Casting vs. 3D Printing
- Historical Context and Evolution of Lost-wax Casting in Jewelry Making
- The Mechanics and Process of Lost-wax Casting for Precision and Detail in Jewelry Design
- Exploring the Modern Innovation of 3D Printing in Jewelry Manufacturing: Materials, Precision, and Personalization
Overview of Jewelry Casting Techniques: Lost-wax Casting vs. 3D Printing
Jewelry casting is an age-old technique that has been refined over centuries to create intricate and detailed pieces. Among the most prominent casting techniques in jewelry making are lost-wax casting and 3D printing. Each method offers unique advantages and has become increasingly popular in the industry for different reasons.
Lost-wax casting, also known as investment casting, is a process that dates back to ancient civilizations. It involves creating a wax model of the desired jewelry piece, which is then covered with a ceramic slurry that hardens into a mold. Once the mold is baked and the wax is removed, molten metal is poured in to take the form of the jewelry. This technique allows for complex designs and fine details to be replicated precisely in metal. The artisanal nature of lost-wax casting imbues each piece with a distinctive character, often appreciated by collectors and connoisseurs of handcrafted jewelry.
In contrast, 3D printing, or additive manufacturing, is a modern innovation that has revolutionized the jewelry industry. This technique involves creating a digital model of the jewelry design using computer-aided design (CAD) software. The model is then printed layer by layer in wax, resin, or metal, directly producing a near-finished product. 3D printing enables rapid prototyping and mass production, making it a versatile option for both bespoke and high-volume jewelry manufacturing. Its precision and efficiency contribute to a reduction in material waste and offer designers the freedom to experiment with complex geometries that were previously unattainable with traditional casting methods. Both lost-wax casting and 3D printing have their place in the realm of jewelry making, with each offering distinct benefits that cater to different needs within the industry.
Historical Context and Evolution of Lost-wax Casting in Jewelry Making
The art of jewelry casting, particularly through the lost-wax casting technique, has a storied history that spans millennia, with its origins believed to date back as far as 3700 BCE. This method, renowned for its intricate and detailed results, involves creating a model in wax, coating it with a refractory material, and then melting the wax out of the mold to allow for the casting of metal within the cavity left behind. The ancient Mesopotamians, Egyptians, and Indus Valley civilizations were among the first to utilize this technique, crafting jewelry that has stood the test of time, both physically and culturally. Over the centuries, lost-wax casting evolved, with significant advancements in the Renaissance era, where it saw a resurgence, leading to an explosion of artistic expression in various art forms, including jewelry making.
Throughout history, the lost-wax casting process has been refined and adapted across different cultures and regions, each bringing their unique touch to this ancient craft. The technique’s evolution is marked by both technological advancements, such as improved materials for molds and waxes, and the incorporation of modern precision engineering. Today, lost-wax casting in jewelry making remains a vital traditional practice in many cultures, alongside being a valued technique in contemporary design, where it competes with and complements modern 3D printing technologies. The continuity and adaptability of this ancient process underscore its enduring significance in the world of jewelry casting.
The Mechanics and Process of Lost-wax Casting for Precision and Detail in Jewelry Design
The intricate process of lost-wax casting is a time-honored technique in the jewelry-making industry, celebrated for its ability to capture fine details and produce precision pieces with consistency. This method involves creating a detailed model of the desired jewelry item using wax, which is then coated in a refractory material, effectively forming a mold. Once the mold hardens, it is heated to melt the wax, leaving behind an empty cavity that is a near-perfect replica of the original design. Molten metal is then introduced into this cavity, filling it and taking the shape of the jewelry piece as it cools. The precision of lost-wax casting lies in its ability to accurately translate the artist’s vision into tangible form, with every curve and intricate detail faithfully rendered in the final product. This technique is particularly favored for elaborate designs that demand a high degree of accuracy, such as those featuring filigree work or delicate engravings. The resulting pieces exhibit a level of craftsmanship and detail that is often challenging to achieve through other jewelry casting methods.
The precision of lost-wax casting is further enhanced by the control it offers over the material properties of the final piece. Artisans can select metals with specific characteristics, including their thermal and mechanical behavior, to meet the demands of different jewelry designs. Whether it’s sterling silver, gold, or platinum, the lost-wax casting process allows for a high degree of customization and quality control, ensuring that the jewelry not only looks exquisite but also withstands daily wear and tear. This technique’s repeatability makes it an excellent choice for mass production while maintaining the integrity of each piece. As such, lost-wax casting remains a cornerstone in the jewelry industry, offering unparalleled detail and precision that continues to be highly sought after by designers and collectors alike.
Exploring the Modern Innovation of 3D Printing in Jewelry Manufacturing: Materials, Precision, and Personalization
3D printing technology has revolutionized the jewelry manufacturing industry, offering a modern alternative to traditional lost-wax casting methods. This innovative approach allows for intricate designs with complex geometries that were once challenging or impossible to achieve through conventional processes. The versatility of materials used in 3D printing is noteworthy, as it encompasses a wide range from precious metals like gold and silver to more cost-effective materials such as resin and bronze. This diversity enables jewelers to experiment with new alloys and textures, pushing the boundaries of design and functionality. The precision afforded by 3D printing is another significant advantage; it ensures that each piece is crafted with exacting standards, leading to a higher level of detail and consistency in the final product. This accuracy not only enhances the aesthetic appeal but also improves the durability of the jewelry.
Furthermore, personalization is at the heart of 3D printing’s appeal in jewelry making. Consumers can now collaborate closely with designers to create bespoke pieces that reflect their individuality and style preferences. The ability to customize a design down to the finest detail without significant changes to production costs or timelines sets 3D printing apart from traditional casting methods. This personal touch, combined with the efficiency and innovation of 3D printing technology, is transforming the way jewelry is designed and produced, making it more accessible and tailored to individual tastes while maintaining high-quality standards. As a result, the jewelry industry is witnessing a shift towards more sustainable and consumer-centric practices, propelled by the advancements in 3D printing technology.