Direct vs Indirect Jewelry Casting: Choosing the Right Technique
Direct and indirect casting techniques play pivotal roles in jewelry making, offering distinct advan…….
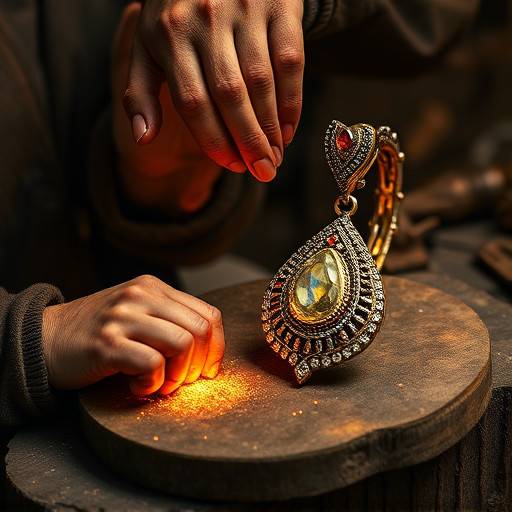
Direct and indirect casting techniques play pivotal roles in jewelry making, offering distinct advantages and applications. Direct casting, involving pouring molten metal into molds, is efficient for complex designs, reproducibility, and mass production due to its precision and speed. Indirect methods, such as lost-wax casting, prioritize flexibility, enabling intricate textures, detailed engravings, and unique custom pieces despite higher costs and time requirements. Effective jewelry casting relies on meticulous preparation, including digital modeling, mold investment, safety protocols, and tool maintenance, ensuring high-quality, aesthetically pleasing outcomes tailored to craft or production needs.
In the realm of jewelry making, understanding casting techniques is paramount. This article delves into the heart of direct casting vs. indirect casting, two fundamental methods shaping today’s vibrant jewelry landscape. From understanding the intricacies of direct casting, exploring benefits and drawbacks of indirect techniques, to selecting the ideal method for your designs, we provide insights crucial for artisans. Discover best practices and common pitfalls to ensure your next jewelry creation is a masterpiece, revolutionizing your approach to this ancient art through effective casting.
- Understanding Direct Casting in Jewelry Making
- The Benefits and Drawbacks of Indirect Casting Techniques
- Choosing the Right Method for Your Jewelry Designs
- Best Practices and Common Pitfalls to Consider
Understanding Direct Casting in Jewelry Making
Direct casting is a fundamental technique in jewelry making, allowing artisans to create intricate designs with precision and detail. This process involves pouring molten metal into a mold, which then hardens to form the desired shape. In jewelry crafting, direct casting is often preferred for its ability to reproduce complex patterns and structures with accuracy. Artisans can work from a master model or design, ensuring each cast piece is an exact replica, making it ideal for creating multiple identical pieces or limited-edition collections.
This method offers several advantages, such as speed and cost-effectiveness for large-scale production while still accommodating the level of detail required in fine jewelry. The direct casting process also enables the use of various metals, from traditional silver and gold to more exotic alloys, catering to different design preferences and wearability needs.
The Benefits and Drawbacks of Indirect Casting Techniques
Indirect casting techniques, often employed in jewelry making, offer a range of benefits while also presenting certain drawbacks. One advantage is their ability to create intricate and complex designs with precision and accuracy. This method allows for the replication of detailed patterns and delicate structures, making it ideal for crafting fine jewelry pieces. By using indirect methods like lost-wax casting or mold-making, artisans can achieve a high level of consistency in production, ensuring each piece is an exact replica of the original design.
However, these techniques might require more time and resources compared to direct casting. The process involves multiple steps, from designing and creating molds to pouring molten metal, which increases the potential for errors or imperfections. Additionally, indirect casting can be costlier due to the materials and labor involved in setting up the intricate molds. Despite these drawbacks, many jewelry makers prefer indirect casting for its versatility, enabling them to produce limited-edition collections with unique, custom designs.
Choosing the Right Method for Your Jewelry Designs
When it comes to jewelry design, selecting the appropriate casting method is a crucial decision that can significantly impact the final product’s quality and aesthetic appeal. Direct casting involves pouring molten metal into a mold, creating a precise replica of the design. This technique is ideal for complex shapes and intricate details, ensuring a high level of accuracy and reproducibility. It allows designers to create multiple identical pieces, making it perfect for mass production and maintaining consistency in their collections.
On the other hand, indirect casting, or lost-wax casting, is a more traditional process where a wax model is first created, coated with ceramic material, and then melted away, leaving an empty mold. This method offers designers greater flexibility, especially when dealing with organic shapes or intricate textures that might be challenging to achieve directly. Indirect casting also allows for the addition of detailed elements like engravings or small components, ensuring jewelry pieces are not only visually stunning but also unique.
Best Practices and Common Pitfalls to Consider
When it comes to jewelry casting, direct and indirect methods each have their own set of best practices and potential pitfalls that artisans should be aware of. For direct casting, ensuring proper preparation is key. This involves accurately designing digital models, choosing the right wax pattern materials, and carefully investing the mold to prevent air bubbles and defects. Skilled artisans will also consider the metal composition and alloying techniques to achieve the desired finish and durability. On the other hand, indirect casting requires meticulous attention to detail in the master model creation process. Sculptors must meticulously carve or 3D print a detailed master model, accounting for potential loss of detail during the investment and casting stages.
Common pitfalls in both methods include contamination of the mold or investment material, which can lead to poor-quality castings. In direct casting, improper preparation can result in porous or weak parts, while indirect casting may produce rough surfaces or lost details. Artisans should also be mindful of safety protocols when handling hazardous materials and equipment, such as furnaces and melting metals, to avoid accidents or health risks. Regular cleaning and maintenance of tools and workspace are essential practices to maintain consistency and quality in jewelry casting projects.