Choosing the Ideal Injection Wax for Precision Jewelry Casting
In the art of jewelry casting, selecting the appropriate type of wax for creating molds is crucial f…….
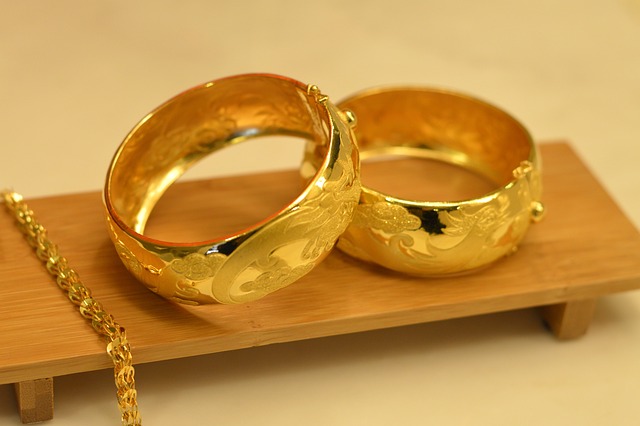
In the art of jewelry casting, selecting the appropriate type of wax for creating molds is crucial for the quality and precision of the final piece. Investment casting wax, which burns cleanly and allows for detailed metal castings without residue, is a popular choice due to its ability to capture intricate details. The refractive index of the wax chosen affects how light interacts with the molten metal, influencing the visual clarity of gemstone settings. Jewelers must consider the wax's dimensional stability to prevent warping during high temperatures. Between traditional paraffin wax and advanced thermoplastic waxes, the decision should be based on the casting operation's efficiency and the jewelry's complexity, with each type offering distinct advantages. LMP waxes like P165 and P295 are favored for their fine detail preservation, while paraffin wax is praised for its cost-effectiveness and good dimensional stability. For more robust designs, PVA and epoxy resins are preferred due to their durability and precision during casting. The choice of injection wax significantly impacts the outcome, with factors like design complexity, investment material compatibility, and desired surface finish all playing a role in achieving a flawless and luminous finish. Understanding the characteristics of each wax type is essential for jewelers and foundry workers to meet casting requirements and produce jewelry with exceptional detail and finish. Safety measures must be observed when handling these materials to ensure a safe working environment, and precise measurements and mixing according to manufacturer guidelines are necessary to avoid defects in the castings. Mastery of these elements ensures that artisans can craft high-quality jewelry with superior finishes, a necessity for excelling in the competitive jewelry market.
exploration of injection wax types reveals their pivotal role in the precision casting of exquisite jewelry pieces. This article delves into the nuances of paraffin and synthetic waxes, highlighting their distinct properties and applications in the art of jewelry making. From the choice of material to the intricacies of casting, we will guide you through selecting the optimal wax type for your creations, ensuring the highest quality and detail in your final designs. Join us as we navigate the diverse landscape of injection waxes essential for mastering the craft of jewelry casting.
- Understanding the Role of Wax Types in Jewelry Casting
- The Variety of Injection Waxes Used in Jewelry Casting
- Comparing Paraffin and Other Synthetic Waxes for Precision Casting
- Tips for Selecting and Using the Right Wax Type for Your Jewelry Casting Needs
Understanding the Role of Wax Types in Jewelry Casting
In the intricate process of jewelry casting, the type of wax utilized plays a pivotal role in determining the success and quality of the final piece. Each wax variant exhibits distinct characteristics that influence the outcome during the casting procedure. For instance, investment casting wax is specifically engineered to create a durable mold. This type of wax burns out cleanly without residue, ensuring that the fine details of the jewelry design are accurately transferred to the metal after casting. Another key consideration is the refractive index of the wax, which affects how light interacts with the molten metal, potentially altering the appearance of gemstone settings and intricate designs. Jewelers must select a wax that maintains dimensional stability under high temperatures to avoid distortion when the mold is heated for casting. This selection process is critical as it can influence the polishing and finishing stages, ultimately affecting the luster and detail of the completed jewelry item.
The choice between traditional paraffin wax or more modern thermoplastic waxes is a decision that significantly impacts the efficiency and precision of the casting operation. Paraffin wax has been the staple for many years due to its compatibility with various investment materials, but it requires precise temperature control during the casting process. On the other hand, thermoplastic waxes offer enhanced workability and allow for rapid prototyping, which is beneficial for complex designs or when multiple pieces are being produced. These advanced waxes can be manipulated with greater ease, facilitating quick modifications to the design without compromising the integrity of the final cast. The decision between these options should be informed by the specific requirements of the casting process and the nature of the jewelry piece being crafted.
The Variety of Injection Waxes Used in Jewelry Casting
In the realm of jewelry casting, the selection of injection wax types is paramount for achieving high-quality, intricate pieces. Artisans and manufacturers have access to a variety of waxes tailored for this purpose, each with its own advantages and optimal applications. Low melting point (LMP) waxes, such as P165 and P295, are popular choices due to their ease of use and detail preservation. These waxes can accurately replicate the fine details of a design, ensuring that the final cast jewelry closely mirrors the original model. Paraffin wax is another common material in the jewelry industry; it offers a cost-effective solution with good dimensional stability during the casting process. On the other hand, polyvinyl alcohol (PVA) and epoxy resins are favored for their durability and high precision, making them suitable for intricate or delicate designs that require a sturdy support during the molten metal pouring stage. Each type of injection wax contributes to the efficiency and success of the casting process, allowing for consistent production of exquisite jewelry pieces with exceptional detail and finish. The choice of wax depends on factors such as the complexity of the design, the investment material to be used, and the desired surface finish of the final product. Understanding the properties and applications of each wax type is essential for jewelers and foundry workers to select the most appropriate material for their casting needs.
Comparing Paraffin and Other Synthetic Waxes for Precision Casting
In the realm of jewelry casting, selecting the appropriate wax type is paramount for achieving precision and high-quality results. Paraffin wax has long been a staple in the jewelry-making industry due to its accessibility and ease of use. It offers a cost-effective solution for creating molds that can withstand multiple casting cycles, making it a favorite among hobbyists and professionals alike. However, its melting point can vary significantly, which may necessitate additional post-processing to ensure the final piece’s integrity.
In contrast, synthetic waxes present alternative options with more consistent melting points and superior durability. These engineered materials are designed to provide a stable foundation for precision casting, accommodating a wide range of metal types and ensuring intricate details are accurately transferred from the wax model to the final metal jewelry piece. Among these, epoxy resin-based waxes and polyvinyl alcohol (PVA) waxes are gaining popularity due to their high precision and resistance to temperature fluctuations during the casting process. When choosing between paraffin and synthetic waxes for jewelry casting, it’s crucial to consider factors such as the complexity of the design, the type of metal being used, and the desired outcome in terms of surface detail and overall quality. Each wax type has its strengths and optimal applications, guiding jewelers to make informed decisions tailored to their specific needs.
Tips for Selecting and Using the Right Wax Type for Your Jewelry Casting Needs
When venturing into the realm of jewelry casting, selecting the appropriate wax type is pivotal for achieving high-quality results. The choice between investment casting wax, epoxy-based wax, and rubber-like wax depends on various factors such as the intricacy of the design, the durability required for the mold, and the compatibility with the metal you intend to use. Investment casting wax, often referred to in the industry as ‘lost-wax casting’ material, is ideal for complex designs with fine details due to its high precision and dimensional stability. It’s a popular choice for delicate pieces that require a detailed reproduction of the original design. On the other hand, epoxy-based waxes offer greater flexibility in terms of working time and can be carved or sawn after setting, which is advantageous for adjustments or repairs post-modeling. They are also more cost-effective than investment casting waxes. For jewelry items that will undergo repetitive molds or require a flexible mold material, rubber-like waxes are the optimal choice due to their elasticity and resistance to deformation. Regardless of the wax type chosen, it’s essential to work with a well-ventilated area and use personal protective equipment to mitigate any health risks associated with the materials. Additionally, ensuring that your jewelry casting process includes a precise measurement and mix of the wax according to the manufacturer’s guidelines will yield the best results and minimize casting defects. By carefully considering these factors and adhering to best practices in jewelry casting, artisans can produce pieces with superior finish and detail, which are key to captivating audiences and standing out in the competitive jewelry market.